Home > Plastic Prototype: Low-Cost Injection Molding Solutions
Details
Details:
Model
Material
Brand
Origin
Application
Booling-Injection Mold-1
P20, 718, S136, 2738 etc
Booling
China
Home Appliance parts
The prototype plastic injection molding technology used by Booling has significant advantages, with fast injection speed and mold opening and closing speed, and can complete the injection, pressure holding, cooling, and demolding processes in a short time. Booling provides prototype plastic injection molding mold solutions, which can help customers trial-produce products or directly carry out low-volume manufacturing, shorten delivery time, and provide faster and more efficient services.
Advantages of prototype plastic injection molding:
- Short molding cycle
- Save raw materials
- Stable product quality
- Good appearance quality
Related Hot Products
Booling provides a low-cost, high-efficiency alternative for industries such as aerospace, automotive, electronics, and medical with prototype plastic injection molding technology, allowing customers to obtain high-precision samples or low volumes of products in a very short cycle, greatly shortening the time for market verification. Although traditional injection molding is suitable for large-scale production, the high mold cost and long development cycle often greatly increase the production cost of enterprises.
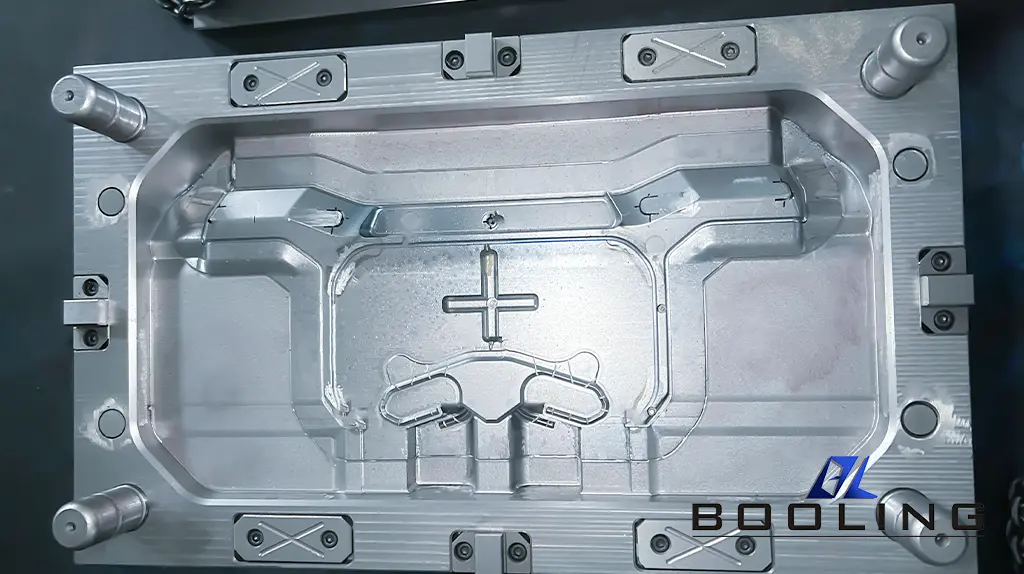
Why Choose Prototype Plastic Injection Molding?
At Booling, we are well aware of the pain points in the product development stage – the traditional mold manufacturing cycle is long, and the cost is high. At the same time, 3D printing is fast, but it is not easy to meet the requirements of mechanical properties and surface accuracy. Therefore, we optimized the prototype injection molding process to make it both economical for rapid prototyping and close to the performance of mass-produced parts. With more than 20 years of excellent injection molding experience from our engineers, we have achieved continuous innovation in the field of prototype plastic injection molding.
In the field of complex mold design and manufacturing, our company can produce the core and cavity of the mold with the help of prototype plastic injection molding technology when designing and manufacturing complex molds, and make precise samples. In this way, manufacturers can promptly discover potential defects and problems in the production process and avoid cost losses in subsequent large-scale production.
Prototype plastic injection molding is based on the rapid prototyping solid model, and uses replication and imitation methods (such as electroplating, metal spraying, composite material casting, precision casting, etc.) to quickly make the main working parts of the mold, such as the punch, die, cavity, and core. This method has high production efficiency and low cost.
Booling uses plastic prototype technology to achieve the advantages of short cycle, simple process, high flexibility, and low molding cost, ensuring accuracy and life to meet customers’ specific functional requirements and having excellent comprehensive economic benefits. Plastic prototypes are fast, convenient, and practical, suitable for new product development, new process and function verification experiments, as well as multi-variety and low-volume production.
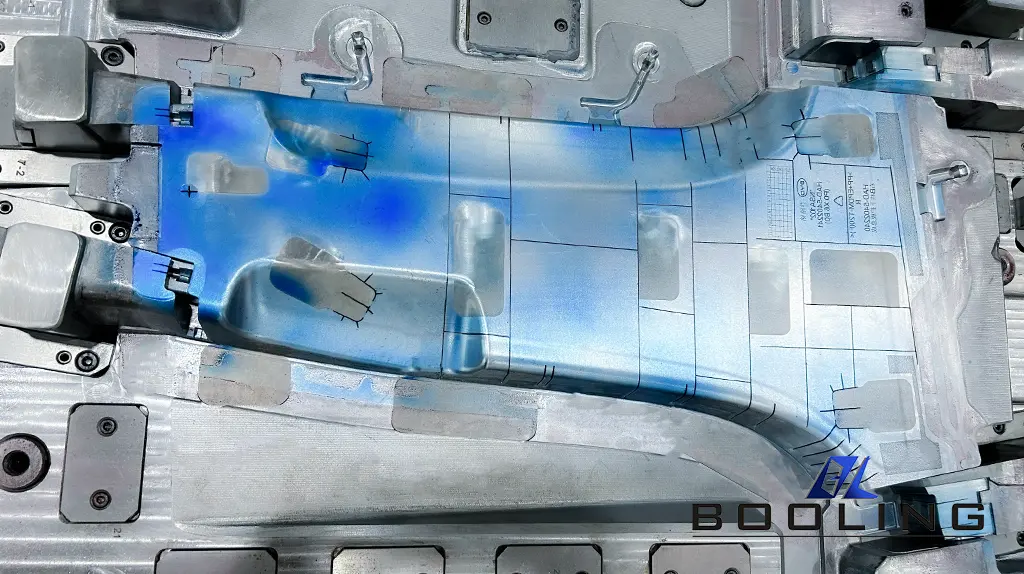
How does Booling achieve low-cost, high-precision prototype plastic injection molding?
Booling uses a special prototype plastic molding process. Traditional steel mold manufacturing usually takes 4-8 weeks, while Booling uses metal spray molding technology to complete the manufacture of high-precision molds within 5-10 days. The core of our process is:
- Booling provides a wide range of raw materials, uses rapid prototyping technology to make sample molds, cleans the surface dirt in time, and applies release agent.
- After the release agent is completely dry, Booling sprays the mold with metal by constantly adjusting and optimizing parameters. During spraying, ensure that the spray gun is always in motion to prevent the coating from overheating and deformation. Booling ensures that the coating thickness is maintained at 2-3mm through continuous testing and optimization to achieve the most uniform state.
- By designing a skeleton structure for the mold, ensure that it can withstand the internal pressure generated during operation.
- Booling uses filling materials with better thermal conductivity, lower solidification shrinkage, and more compression and tensile resistance, such as a mixture of epoxy resin and metal powders, such as aluminum powder and aluminum particles.
- After the mold is demolded, the manufacturer needs to clean the release agent remaining on the surface of the metal coating, and then polish the mold according to different needs to facilitate subsequent production.
These data can be directly used for subsequent mass production mold development, helping customers to smoothly transition to large-scale production and reduce the cost of repeated debugging.
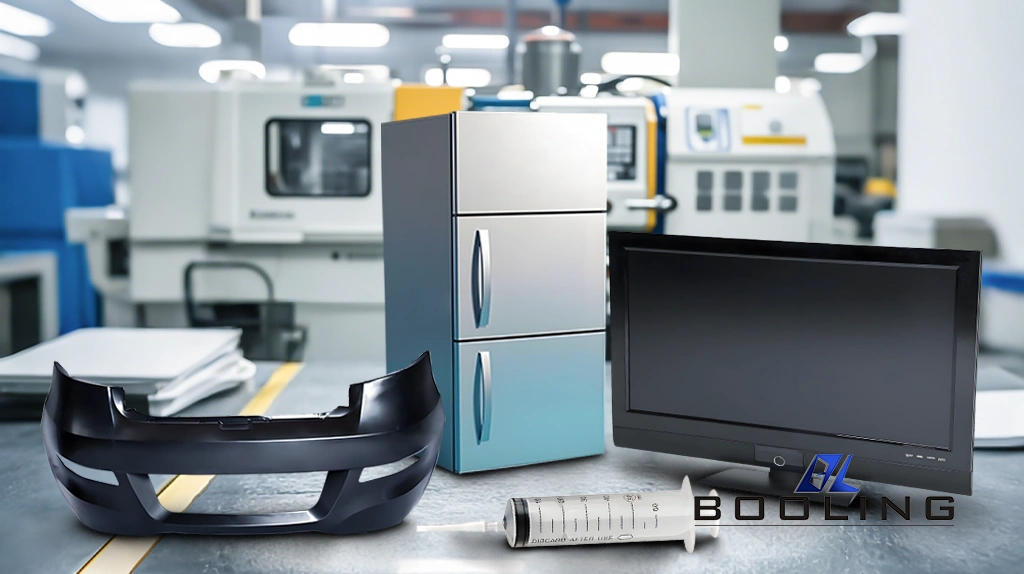
Industrial Applications of Prototype Plastic Injection Molding
In the field of precision manufacturing, plastic prototype technology can help manufacturers quickly manufacture samples, realize trial production, and small-batch production. Booling can arrange delivery as soon as the mold is ready, helping customers to start production faster and meet customer market needs.
- Automobile Field: It can trial-produce parts during the development of new automobile products, quickly make various samples, and realize low-volume production.
- Electronic Equipment Field: It can make shells of electronic products such as mobile phones and computers, and can also mold connectors, radiators, etc., in low volumes.
- Aerospace Field: Aerospace has high requirements for parts, and prototype plastic injection molds can be used to manufacture molds for these parts, realize lightweight production, and improve fuel efficiency.
- Home Appliance Field: Various parts molds of large home appliances such as refrigerators, air conditioners, and washing machines can be manufactured with rapid molds.
- Medical Field: It can be used to manufacture shells of various medical devices, as well as disposable medical supplies such as syringes and infusion sets.
At Booling, we believe that “fast trial and error” is the shortcut to product success, whether it is:
Concept verification stage: Need 1-5 appearance samples?
Functional testing stage: Need 50-500 small batches for trial production?
Mass production transition stage: want to optimize process parameters to reduce scrap rate?
Our “3D printing + prototype plastic molding” hybrid mode can provide you with flexible options:
Extremely fast response: 72 hours to deliver the first version of the sample
Cost controllable: mold cost is only 20%-30% of traditional steel molds
Seamless mass production: provide a complete DFM (manufacturability analysis) report
Contact the Booling team now for free technical consultation and quotation! Let us use smarter prototype solutions to help your product development win at the starting line.
Automotive Mold Related Content
Applied’s expertise in modifying materials at atomic levels and on an ihdustrial scaleenables our customers to transform possibilities into reality.