Home > Key Points of HDPE Blow Molding
Details
Details:
Model
Material
Brand
Origin
Application
Booling-Blow Mold-1
P20, 718, S136, 2738 etc
Booling
China
Home Appliance parts
Booling controls the molding quality of HDPE products by continuously improving the parameters in HDPE blow molding technology, such as screw speed, melt temperature and extrusion pressure, and achieves precise control of product wall thickness, meeting the precision needs of manufacturers in the fields of automotive parts, electronic equipment, etc. As an innovator who has been deeply involved in blow molding technology for many years, Booling has always been committed to providing customers with high-precision products within a tolerance of ±0.01mm through parameter optimization, mold design, and material science breakthroughs, while achieving a perfect balance between production efficiency and product performance.
Advantages of HDPE blow molding:
- Good material properties
- Continuous production
- Cost-effective
- Easy to control product wall thickness
- Excellent surface quality
Related Hot Products
HDPE blow molding technology has a high production speed. Booling continuously improves production processes and parameters, optimizes the quality of molded products, and continuously breaks through the precision limitations in the field of blow molding products, ensuring that HDPE blow molding products can have both physical and chemical properties, and controlling the molding tolerance within ±0.01, providing customers with higher quality and performance HDPE blow molding solutions.
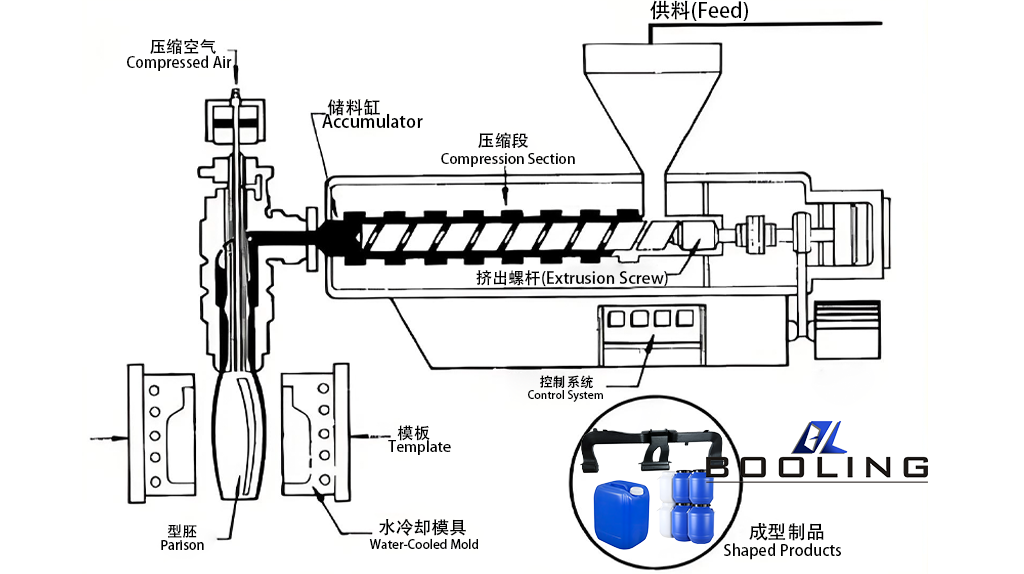
HDPE Blow Molding Principle
In Booling’s view, blow molding is not a simple “heating-inflation-cooling” process, but a systematic project that requires multi-dimensional coordination. Our technical team intervenes in the control from the raw material selection stage:
- Raw Material Preparation: According to the mechanical requirements of customer products (such as tensile resistance or environmental stress cracking resistance), we select HDPE particles with different melt flow index (MFI) and molecular weight distribution, and eliminate moisture interference through pre-drying treatment.
- Parison Extrusion: Put the prepared raw materials into the extruder, and melt and extrude the raw materials into a tubular parison through the rotation of the screw. At this time, Booling’s engineers will pay attention to parameters such as temperature and screw speed to ensure the quality of the parison.
- Mold Closing: Put the extruded parison into the blow mold quickly and clamp it.
- Blow Molding: Introduce compressed air to expand the parison and fit the inner wall of the mold.
It is particularly worth emphasizing that our ability to predict shrinkage and handle deformation has become the key reason for customers to choose Booling. HDPE will shrink anisotropically after cooling (differences in shrinkage rates in length, width, and thickness). We combine CAE simulation with measured data to reserve shrinkage margins during the mold design phase to ensure that the final dimensions match the drawings by more than 99%.
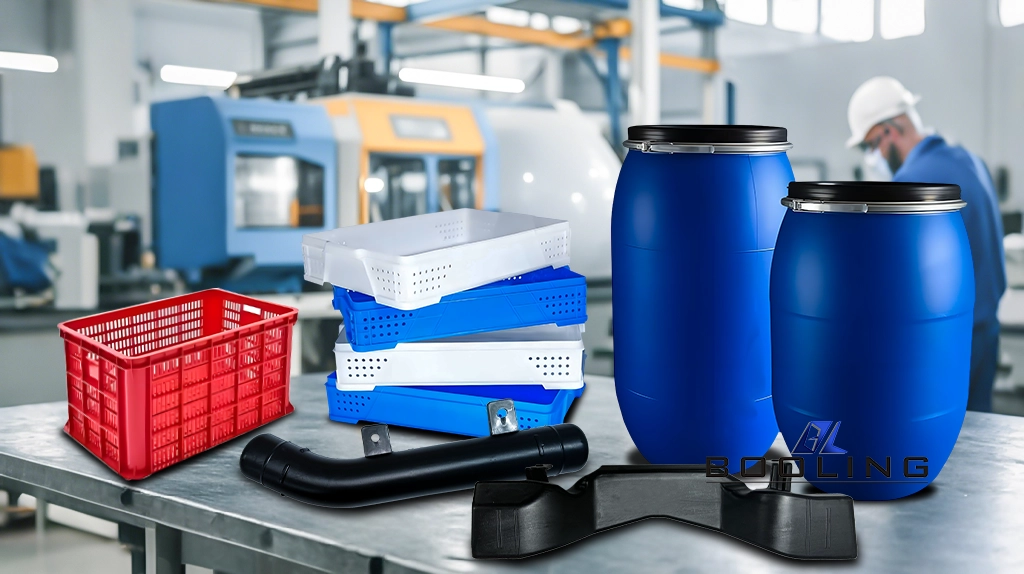
Key Points of HDPE Blow Molding
“In the field of electronic equipment accessories, customers have proposed a wall thickness tolerance of ±0.02mm, which is almost 1/5 of the industry standard value.” Booling’s chief engineer mentioned, “By optimizing the layout of the cooling water channel and introducing infrared temperature monitoring, we not only achieved this goal, but also shortened the molding cycle by 15%.”
This breakthrough stems from our extreme control of four key dimensions: We deeply analyze factors such as the melt flow index, density, and molecular weight distribution of HDPE to achieve precise matching of raw materials and products to ensure molding quality.
1.Select high-quality mold steel, such as P20, 718, etc. The mold can also be specially customized according to customer requirements.
2.Booling engineers accurately control the temperature of each section of the extruder to ensure that the HDPE particles can be fully melted and avoid carbonization. By planning a reasonable cooling time and adopting a segmented cooling method, the cooling efficiency is ensured.
3.Maintain appropriate blow molding pressure to avoid cracking due to long inflation time of the parts or unclear patterns due to insufficient time.
Booling has determined the optimal molding cycle, cooling time, pressure, and temperature settings through repeated trials and optimization, and has demonstrated excellent reliability in industries such as piping systems and packaging containers.
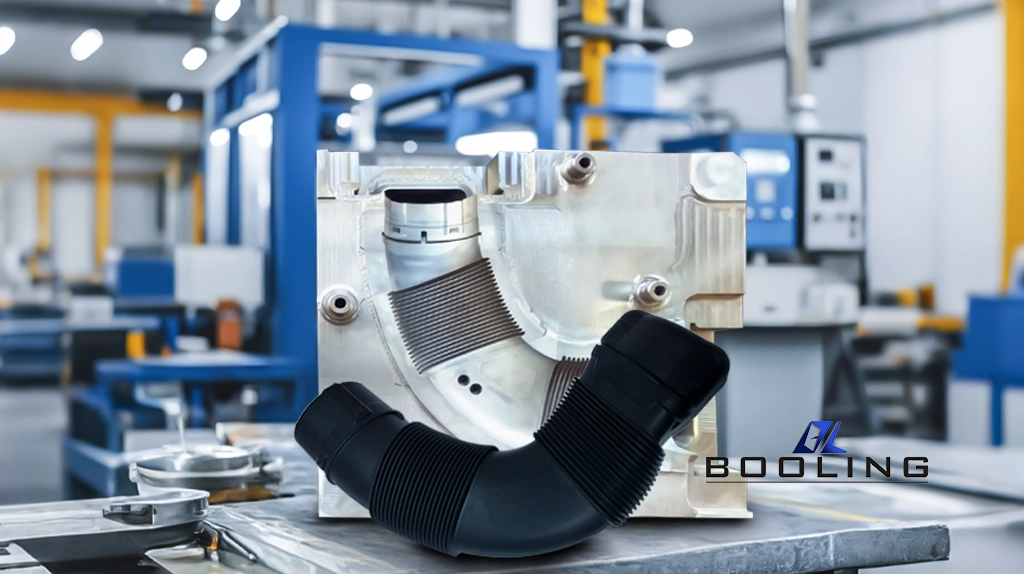
Key Parameters of HDPE Blow Molding
In the field of HDPE blow molding, precise control of shrinkage can ensure that the size of the blow molded part is completely consistent with the designed mold cavity, ensure the stability of processing, and improve the product qualification rate.
-Definition of Shrinkage
The shrinkage of HDPE blow molding usually refers to the ratio of the mold cavity size to the blow molded part size after processing at room temperature for 24 hours.
-Factors Affecting Shrinkage
The time and type of materials used for HDPE blow molding, the temperature set during blow molding, the thickness, size, and volume of the parts, etc.
The size of the shrinkage depends on the structure, wall thickness, and quality of the HDPE workpiece. The shrinkage in the length, width, and thickness directions of the workpiece is usually different. Booling conducted pre-measurement and simulation analysis in the design stage, and reserved shrinkage space to ensure that the product meets the quality requirements.
For some products with higher precision requirements, Booling will determine the processing process and structural settings according to the customer’s equipment, molds, materials, and other requirements, and use tools such as shaping frames to obtain more accurate products.
We have developed air conditioning ducts for a new energy vehicle company, and their noise reduction and thermal insulation indicators exceeded the national standard by 20%. This is not accidental, but stems from the full-link coordination of materials, processes, and design: from molecular chain orientation regulation to mold line strength optimization, every decision made by Booling points to the actual performance of the end product.
Contact the Booling technical team now to get a free mold molding process evaluation report immediately! Let us use millimeter-level craftsmanship to help your product gain an advantage in the market.
Automotive Mold Related Content
Applied’s expertise in modifying materials at atomic levels and on an ihdustrial scaleenables our customers to transform possibilities into reality.