Home > What is EVA Foam Injection Molding ?
Details
Details:
Model
Material
Brand
Origin
Application
Booling-Injection Mold-1
P20, 718, S136, 2738 etc
Booling
China
Home Appliance parts
The EVA foam products produced by Booling not only feature a uniform and fine cell structure but also employ a strict three-point test method to ensure the performance stability of each batch of products. We believe that “excellent EVA foam products are not simple material molding, but the art of precise control of cell structure, density distribution, and mechanical properties.” Our EVA injection molding mold uses a patented gradient temperature control system to ensure that the foaming agent can be decomposed more evenly and the cell diameter can be controlled within the range of 0.1-0.5mm.
Advantages of EVA foam injection molding:
- Excellent flexibility
- Cushioning and weather resistance
- Non-toxic and harmless
- Good chemical resistance and stability
Related Hot Products
True customization of EVA foam injection molding is not a simple size adjustment, but a full-process innovation from material formulation, and mold design to process parameters. We pay special attention to: “Mold is the core of EVA molding. Booling uses five-axis precision machining combined with laser measurement technology to ensure that the molding accuracy reaches ±0.02mm, which is the basic guarantee for achieving stable foaming quality.”
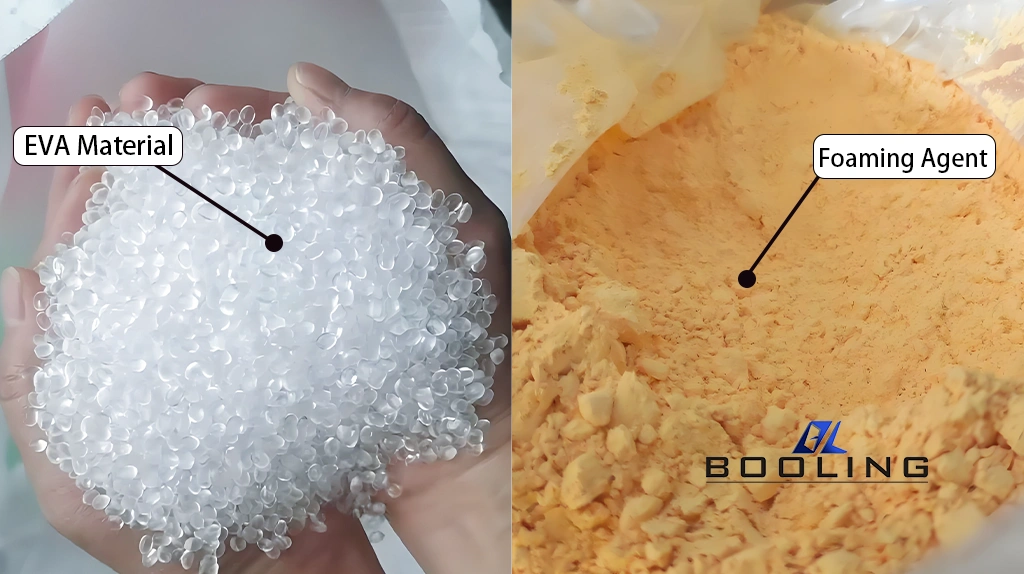
Detailed Explanation of EVA Foam Injection Molding Process
We believe that: “The real advantage of EVA foam injection molding technology is not only reflected in the accuracy of the equipment but also in the deep understanding and precise control of the foaming dynamics process.” We not only have the ability to manufacture molds but also can provide users with a full-process, high-quality one-stop solution.
- Our company uses an advanced high-precision metering system to control the ratio error of EVA raw materials and foaming agents to about ±0.01%.
- Through the independently developed formula optimization technology, the gas release rate of the foaming agent is adjusted according to the needs of different products to achieve a stable foaming effect.
- After the raw materials are mixed, they enter the melting and plasticizing stage of the injection molding machine. Booling’s injection molding equipment is equipped with high-precision temperature sensors and pressure control systems, which can accurately control parameters such as barrel temperature and screw speed, and can effectively avoid surface defects and performance defects.
- After the plasticized EVA raw materials and foaming agents are mixed, they are injected into the mold cavity at high speed. Chemical foaming agents are quickly decomposed at high temperatures, while physical foaming agents expand rapidly when the pressure drops.
- In the foaming and expansion stage, Booling’s intelligent control system plays an important role. The mold pressure can be flexibly adjusted between 5~25MPa to avoid appearance defects and meet customer requirements for appearance performance.
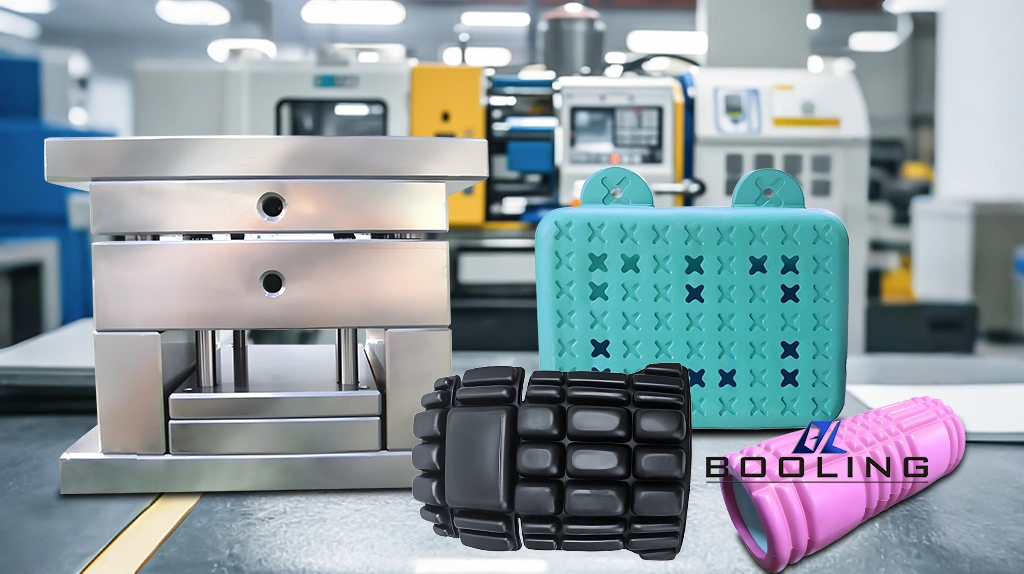
EVA Foam Injection Molding Characteristics
In the field of EVA foam injection molding, we not only provide equipment but also provide complete solutions based on deep process understanding. From raw materials to finished products, every link embodies our 20 years of technical accumulation, which is the core competitiveness that Booling can continue to lead the development of the industry.
- It has excellent water resistance, creates a closed cell structure, does not absorb water, is moisture-proof, and has good water resistance. It is widely used in the fields of construction and packaging.
- It has excellent corrosion resistance and is resistant to corrosion by seawater, grease, acid, alkali, and other chemicals. The material has passed strict safety testing and has the characteristics of antibacterial, non-toxic, odorless, and pollution-free.
- It has excellent processability and can achieve precise molding of various complex shapes.
- It has a good shock absorption effect. When its terminal products are impacted by external forces, they can quickly absorb and disperse energy and maintain good buffering performance.
- It can maintain stable and reliable performance in severe cold and high-temperature environments.
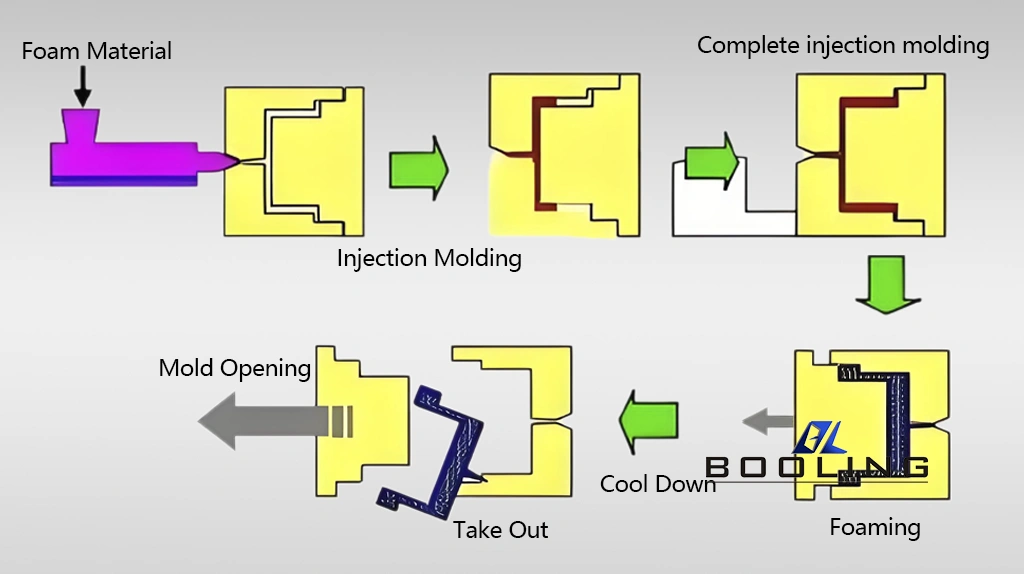
The Principle of EVA Injection Molding
Booling has rich experience in polymer material processing and provides customers with comprehensive solutions for chemical foaming and physical foaming. We believe that: “Only by truly mastering the principle of foaming can we break through the process bottleneck and achieve a leapfrog improvement in product performance.”
- Chemical Foaming Technology
Adding chemical foaming agents, such as azodicarbonamide and sodium bicarbonate, decomposes at high temperatures to produce gas, and the melt expands to form bubbles and finally forms a honeycomb foaming structure inside the product.
Chemical foaming technology has significant advantages in process control and product performance. Booling has independently developed efficient dispersion processes and special equipment to ensure that the foaming agent is evenly dispersed at the micron level in the polymer matrix.
- Physical Foaming Technology
Physical foaming technology uses the solubility of gas in polymer materials to achieve foaming with pressure changes.
Physical foaming technology has environmental protection characteristics. There is no chemical reaction involved in the entire processing process, and there is no chemical residue, which is environmentally friendly. Using physical foaming technology, ultra-fine foaming structures can be prepared, and the end products have excellent mechanical, thermal insulation and cushioning properties.
At present, Booling’s innovative foaming technology has been successfully applied to eight fields such as sports shoes, automotive interiors, and electronic packaging, serving more than 300 well-known brands around the world. We sincerely invite partners from all industries to visit us and explore the various possibilities of EVA foaming technology. Contact our technical consultants now to get exclusive 1v1 solutions!
Automotive Mold Related Content
Applied’s expertise in modifying materials at atomic levels and on an ihdustrial scaleenables our customers to transform possibilities into reality.