Home > Injection Molding > Mold Surface Treatment
Mold surface treatment refers to the technology of forming a strengthening layer or functional layer on the surface of the mold substrate through physical, chemical or mechanical methods to improve key properties such as wear resistance, corrosion resistance and demolding properties.
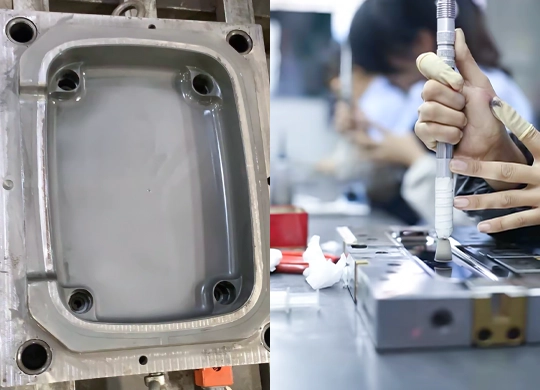
Why choose BOOLING ?
Customize your mold surface treatment solution
Molds are key molding tools in the manufacturing and industrial fields. The surface quality of the mold determines the appearance, surface accuracy and demolding performance of the product. Booling provides customers with customized surface treatment solutions such as anodizing, mirror polishing, frosting, leather grain, etc. for molds of different materials such as metal and plastic based on parameters such as product characteristics, mold cost, appearance requirements, etc. to meet customers’ specific needs.
We provide surface treatment solutions for metal, plastic, and other molds, tailor-made for customers’ products, and provide a wider range of choices. We are always customer-oriented and have built a complete production system. From process solution design to finished product delivery, we can provide you with full technical support and quality assurance. Choose Booling to achieve the pursuit of ultimate craftsmanship and escort customers’ production.
Key advantages of Booling mold surface treatment
Mold surface treatment reference table
Booling has more than ten years of experience in mold processing, and has core mold surface treatment technologies such as surface hardening, nickel plating, hard chrome plating, mirror polishing, frosting, and leather graining, providing you with substantial help to improve the surface quality and aesthetics of the terminal product and solve manufacturing problems.
Surface treatment categories | Specific methods | Features | Advantages | Typical Applications | Special treatments |
---|---|---|---|---|---|
Surface hardening treatment | Nitriding treatment | Infiltrate nitrogen atoms into the mold surface to form a nitrided layer | Hardness can reach HV900-1200, small deformation, improve mold wear resistance | Suitable for molds with high friction coefficient materials | No subsequent quenching is required |
Carburizing treatment | Carbon atoms are infiltrated into the surface of the low-carbon steel mold, forming a high-hardness layer after quenching, and the internal toughness is maintained | Strong wear resistance and impact resistance | Molds such as automobile bumper molds that need to withstand large impact loads | Heat treatment deformation is large, and subsequent finishing is required | |
Quenching + tempering | Quickly cool the mold after heating, and temper at low temperature to eliminate stress | High surface hardness, improve the compression resistance of the mold | Suitable for small and medium-sized molds, such as electronic component injection molds, etc. | More precise control of process parameters is required | |
Coating treatment | Hard chrome plating | Electroplating in a specific electroplating solution to deposit a layer of hard chrome on the surface | Improve the surface wear resistance of the mold, improve demoulding performance and corrosion resistance | Large molds such as home appliance housings | The chromium layer may become brittle |
Nickel plating | Using chemical reduction reaction, a layer of nickel-phosphorus alloy is deposited on the mold surface | Improve the corrosion resistance of the mold and extend the service life of the mold | Plastic molds, rubber molds, etc. | It is a chemical reaction | |
Surface finishing treatment | Mirror polishing | The mold is polished by sandpaper, abrasive paste, electrolysis, ultrasound and other means to achieve a mirror effect | The mold mirror polishing has a very high finish, and the roughness can usually reach Ra0.01-0.02μm, and there are basically no defects visible to the naked eye | Suitable for molds with high surface gloss requirements such as automotive parts, daily necessities, electronic products, and home appliance shells | It needs to go through multiple processes such as rough polishing, semi-finishing polishing and fine polishing, which requires higher experience and technology of engineers |
Frosting | Through mechanical grinding, sandblasting or chemical corrosion, a tiny but uniform concave and convex structure is formed on the mold surface to change the light reflection effect of the mold | Make the mold surface matte and non-slip, and improve the aesthetics of the terminal product | Electronic equipment housing, household goods, cosmetic packaging, automotive parts and other molds to meet the design requirements | Can cover the surface defects such as welding marks and shrinkage generated during the production process | |
Leather grain | Through chemical corrosion, laser engraving and other processes, specific textures and patterns are formed on the surface of the mold, giving the product better visual effects and touch | Improve the aesthetics and texture of the terminal product and meet functional needs | Automotive parts, electronic and home appliance molds, daily necessities and packaging molds, medical equipment molds, etc. | Various textures. Such as leather grain, metal texture, etc. |