Home > Polycarbonate Custom Injection Molding Solutions
Details
Details:
Model
Material
Brand
Origin
Application
Booling-Injection Mold-1
P20, 718, S136, 2738 etc
Booling
China
Home Appliance parts
As an expert in polycarbonate injection molding, Booling emphasizes that in polycarbonate processing, key parameters such as melt temperature, injection speed, and mold temperature must be strictly controlled to avoid defects, including stress cracking and silver streaks, in the products. The company ensures that every polycarbonate product can achieve optimal performance through innovative process solutions and strict quality control. With its excellent mechanical properties, optical transparency, thermal stability, and flame retardant properties, polycarbonate materials meet the needs of manufacturers in various fields, including automobiles, electronics, and medical care.
Advantages of polycarbonate injection molding:
- High strength and toughness
- Good transparency
- Extreme temperature resistance
- Chemical corrosion resistance
- High production efficiency
Related Hot Products
Polycarbonate injection molding needs to take into account both material properties and process parameters. Booling has accumulated years of industry experience and believes that only through the precise control of both can molding optimization be achieved. We firmly believe that through scientific material selection and process optimization, we can give full play to the performance advantages of polycarbonate and create greater value for customers. As a professional service provider in the field of polycarbonate processing, our company provides customized solutions for manufacturers in different industries to achieve product performance upgrades and manufacturing cost optimization.

Key Advantages of Polycarbonate Injection Molding
Booling always adheres to the concept of “materials are the basis, technology is the key”, and helps customers solve technical problems in polycarbonate injection molding through continuous innovation, to achieve dual improvement of product performance and production efficiency. Our engineering team can provide customers with full-process technical services from design optimization to mass production support, ensuring that each project can meet the best quality standards. We strictly follow the injection molding process to provide users with higher-quality solutions.
Polycarbonate material has excellent transparency, and the light transmittance can reach more than 90%, which can achieve a visual effect similar to flat glass, and meet the requirements of precision optical instruments, lamps, display screens, and other products with extremely high light transmittance.
Polycarbonate has excellent heat resistance and can maintain long-term stable use in an environment of 120°C, which is suitable for processing in industry, electronic equipment, etc.
While achieving lightweight processing, it can ensure high-strength processing. Booling combines advanced mold design and process control technology to control the dimensional accuracy of the terminal product within ±0.05mm。
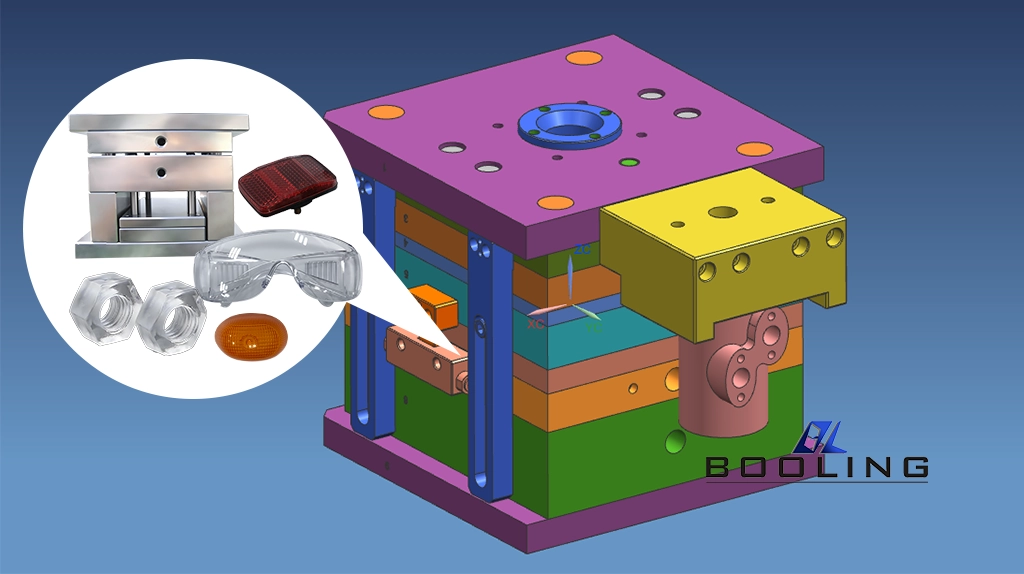
Polycarbonate Injection Molding Mold Design
Polycarbonate injection molding has comprehensive performance. Booling has a strong R&D team and can realize customized mold design and processing according to the special needs of customers. We believe that “excellent mold design is the key to ensuring the performance of polycarbonate products.”
Booling selects suitable mold steels such as 718H, S136H, 45#, P20, etc. according to customer needs and cost budget.
Polycarbonate plastic melt has high viscosity. Engineers usually set the main channel with a larger taper and smaller inner wall roughness to avoid melt retention.
Booling sets point gates, latent gates, or fan gates according to the needs of user products to provide users with customized products with higher aesthetics.
The shrinkage rate of polycarbonate is between 0.5% and 0.8%. When designing the core and cavity, a certain margin needs to be reserved.
Set a suitable demolding slope to prevent scratches on the product during demolding.
Polycarbonate is sensitive to mold temperature. Booling ensures product performance through precise temperature control. The mold temperature is usually set at 80~120℃, and a cooling system is used to prevent local temperature differences from causing product deformation.
Polycarbonate is prone to cracking due to stress, and local stress needs to be avoided during demolding. Booling provides ejector pin and push plate ejector solutions.
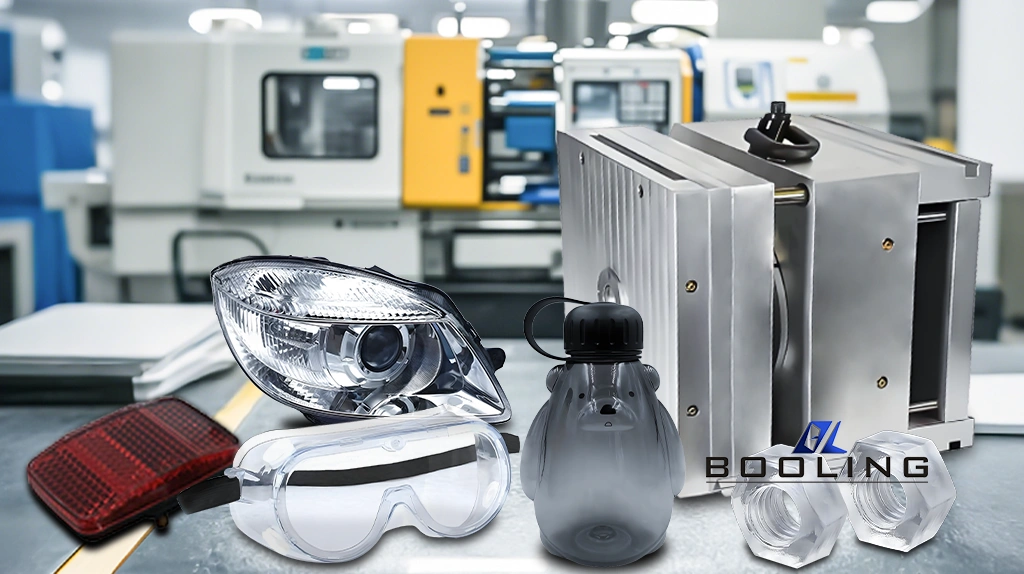
Reasons to Choose Booling polycarbonate Injection Molding
For 15 years, we have focused on the research development and application of polycarbonate molding technology, providing customers with trustworthy and comprehensive services. Booling has rich experience in polycarbonate injection molding and has received unanimous praise from users in the field of polycarbonate molds and products.
Our company has mastered the key parameters of polycarbonate injection molding, which can significantly reduce the possibility of product defects.
Our company adopts a hot runner system, multi-stage injection process, and modular design to achieve fast and stable production of products.
Designers and engineers can handle complex structures and easily solve design problems such as thin walls, transparency, and inserts.
By optimizing mold design and adopting design solutions such as one mold and multiple cavities, we provide cost-balancing solutions.
Through national testing standards, our company has the qualifications to produce products in the fields of automobiles, medical care, etc.
Welcome to communicate with our engineers online at any time to start your polycarbonate injection molding optimization journey! Booling looks forward to working with you to create excellent products together.
Welcome to communicate with our engineers online at any time to start your polycarbonate injection molding optimization journey! Booling looks forward to working with you to create excellent products together.
Automotive Mold Related Content
Applied’s expertise in modifying materials at atomic levels and on an ihdustrial scaleenables our customers to transform possibilities into reality.