Home > Car Grille Mold: Special Design Points
Details
Details:
Model
Material
Brand
Origin
Application
Booling-Automotive Mold-1
P20, 718, S136, 2738 etc
Booling
China
Automotive parts
The car grille is the core component of the front face of the car, and its mold design directly affects the precision and quality of the product. Booling’s technical experts pointed out: “Modern car grille mold design has entered a new stage driven by digital simulation, and high-fidelity CAE analysis can significantly reduce the cost of mold testing.” Our company relies on professional 3D design software (such as NX/Moldflow) to build a high-precision digital model of the car grille mold and conduct multi-physics field coupling simulation of the pouring system, cooling water channel, and molding process.
Advantages of grille mold processing:
- High precision
- Flexible design
- Strict tolerance control
- Consistent production
Related Hot Products
Booling has more than 10 years of rich experience in the design and manufacturing of automotive grille molds and has customized and developed high-quality molds for many automakers. We always adhere to customer-oriented, effectively shortening the mold development cycle to more than 30%. Through 3D modeling and analysis technology, we provide users with a one-stop solution from design and development to production and manufacturing to ensure the feasibility and accuracy of mold design. Booling’s research data shows that the use of our integrated solution can reduce the product defect rate by 45% and increase mold life by more than 20%. We provide one-stop services from design and development to production and manufacturing to ensure the high feasibility, high precision, and stable mass production capacity of the mold, helping customers gain an advantage in the fierce market competition.
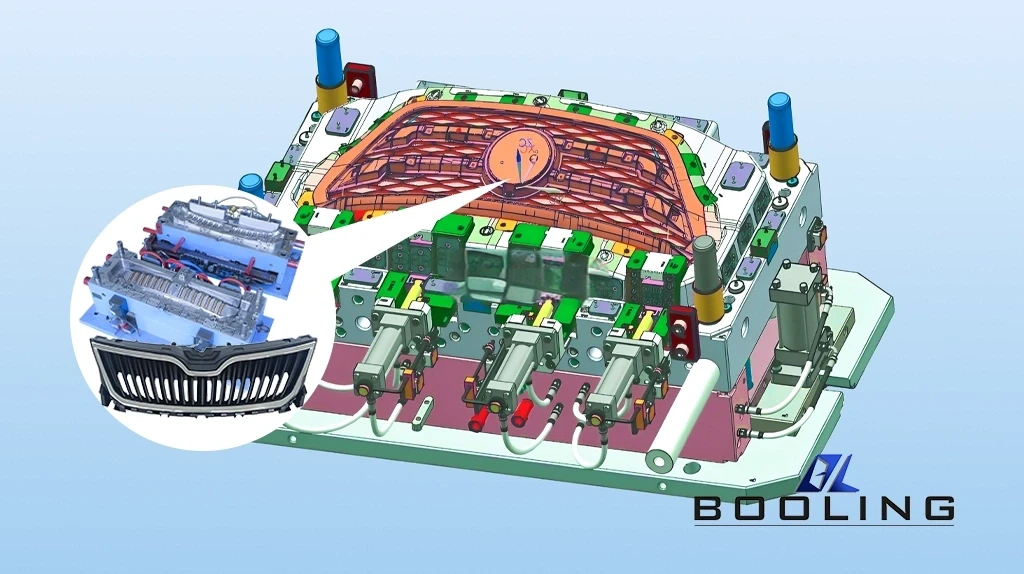
3D Design and Analysis of Car Grille Mold
The design of automobile grille molds is usually more complicated. UG NX design software integrates CAD/CAM/CAE functions and has powerful surface modeling capabilities, which can create automobile grille molds with higher precision and reliability for users. The advantages of UG NX software in complex surface modeling make it the preferred tool for auto grille mold design. Its integrated CAD/CAM/CAE functions can significantly improve design efficiency and molding quality. We use UG NX design software to develop automobile grille molds and give full play to its powerful surface modeling capabilities. Booling’s practical data shows that compared with traditional design methods, the use of UG NX can improve the surface accuracy of grille molds by 40% while reducing 30% of design rework. Through the simulation analysis module integrated into the software, we can accurately predict and optimize the molding performance of the mold, creating automobile grille molds with higher precision and reliability for users.
-CAD Design: Carry out 3D modeling of automobile grille molds in the CAD module, and use modeling tools to create each component precisely to form a complete mold structure. Use the assembly modeling function to perform virtual assembly and interference inspection on each component of the mold.
-CAE Analysis: Import the mold model completed in the CAD module directly into the CAE module, and analyze it according to the usage requirements and actual processing requirements, such as mold flow analysis and processing feasibility analysis, to predict possible defects.
-CAM Programming: Optimize the mold model according to the analysis results in the CAE module, import the model into the CAM module for CNC programming, generate appropriate tool paths and processing parameters, ensure the accuracy of the processing process, and avoid manual errors.
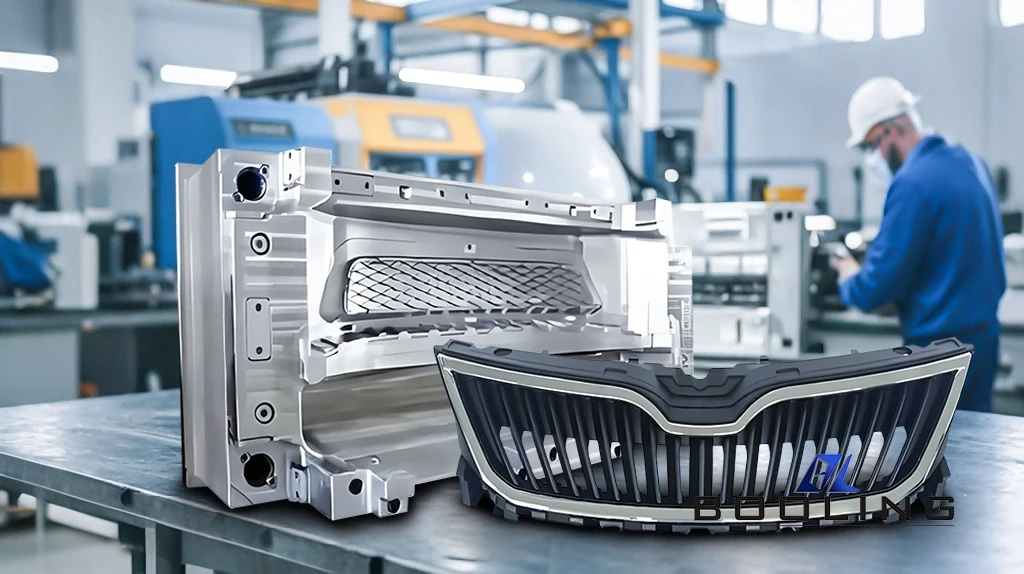
Design Points of Automobile Grille Mold
During the design process, automobile grille molds need to consider the overall shape of the car and the structure of each component system, ensure the quality of the final product, and provide customers with a more complete solution. Booling’s mold experts emphasized: “Under the trend of integrated design of new energy vehicle grilles, the multidisciplinary collaborative function of NX software helps us achieve a perfect balance between structure and aesthetics, which is difficult to achieve with traditional design methods.” We continue to deepen the application of UG NX to ensure that each mold project can meet the strict quality standards of the OEM.
Analyze the structural points, dimensions, and precision requirements of the automobile grille. If there are more complex hollow structures and slender strips, it is necessary to focus on the molding method and demolding mechanism of these parts.
Clarify the plastic raw materials used in automobile grilles, such as ABS and PP. There should be no obvious defects such as weld marks and gas marks on the surface of the product. When designing the mold, the shrinkage rate of the material must be considered, and sufficient shrinkage margin must be reserved to ensure the dimensional accuracy of the product.
As an important front face exterior part, the automobile grille has high requirements for appearance. It usually adopts the form of a pointed gate or latent gate to reduce gate marks during processing and improve appearance quality.
Automobile grilles are usually larger products, and the location and number of cooling water channels need to be reasonably distributed to ensure uniform cooling of all parts and reduce product deformation or impact on structural strength.
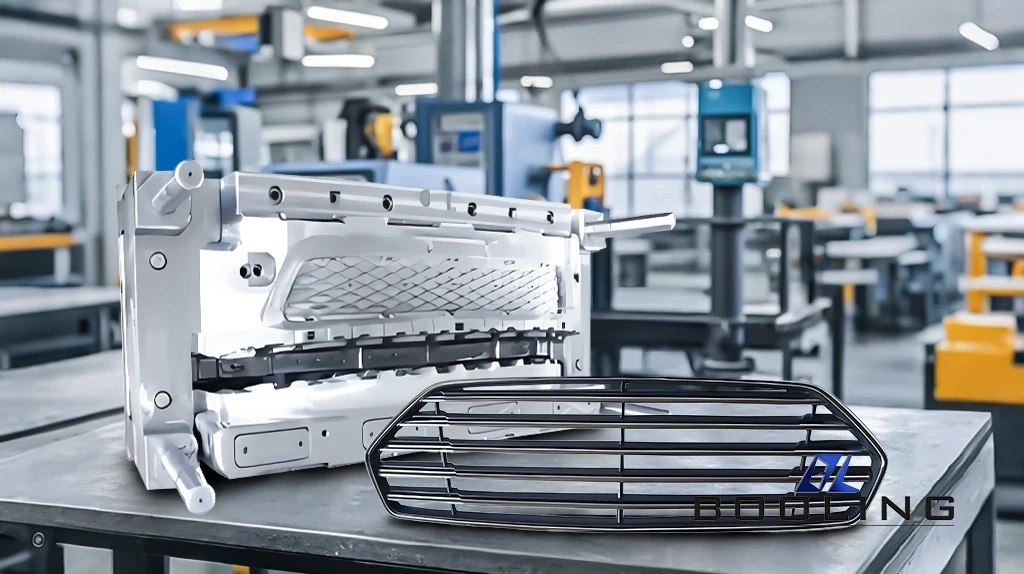
Design Process of Automobile Grille Mold
Booling provides product analysis, design, and simulation of automobile grille molds, and conducts comprehensive analysis and evaluation from the aspects of functional requirements, precision standards, and appearance quality. Based on the industry-leading CAE analysis technology, we conduct a comprehensive evaluation from three dimensions: functional requirements, precision standards (±0.05mm), and appearance quality (Class A surface). Booling’s case data shows that through our multi-physics field coupling analysis, the first mold test pass rate of customer products has increased to 92%, far exceeding the industry average.
Communicate with various departments and customers to clarify the function, precision, and appearance requirements of the automobile grille, understand the installation position on the car, and the matching requirements with other parts.
Import the 3D model data of the automobile grille into UG and other software to check the integrity of the model to avoid problems such as broken surfaces and overlapping surfaces. And determine the type of mold, the number of cavities, and the processing technology. Use the parting tool in UG to establish a reasonable parting surface according to the structural characteristics of the grille and the production batch to ensure smooth demolding,
Design the mold cavity, core, slider, and core pulling mechanism, pouring system, and cooling and demolding system according to the parting surface.
Assemble the designed mold. During the assembly process, ensure that the assembly position of each part is accurate and meets the requirements of matching clearance and precision.
Simulate the opening and closing movement of the mold in UG to check whether the opening and closing of the mold are smooth, there is no abnormal sound, and there is no collision or interference between each component.
Automotive Mold Related Content
Applied’s expertise in modifying materials at atomic levels and on an ihdustrial scaleenables our customers to transform possibilities into reality.