Home > Automotive Pillar Mold: 3D Printing Technology & CNC Machine Tool Processing Technology
Details
Details:
Model
Material
Brand
Origin
Application
Booling-Automotive Mold-1
P20, 718, S136, 2738 etc
Booling
China
Automotive parts
In the design and processing of automotive pillar molds, Booling uses innovative 3D printing technology and CNC machine tool processing technology to provide users with more precise collaborative solutions. Through advanced simulation analysis technology, our engineering team can accurately optimize the key structure of the mold, including gate location, cooling system layout, and ejection mechanism design. Booling’s latest case data shows that after adopting our collaborative manufacturing solution, the dimensional stability of the customer’s product reaches the 0.01mm tolerance requirement, and the surface roughness is controlled within Ra0.4μm.
Advantages of automobile pillar mold processing:
- Realize lightweight production
- High appearance quality
- Have safety performance
- Strict quality control
Related Hot Products
With rich industry experience and successful cases, Booling has provided customized car pillar mold solutions for more than 50 global automotive brands. While using traditional processing technology, we have also utilized advanced 3D printing and CNC processing technologies to achieve personalized customization and high-quality production of molds and to achieve safe and lightweight production of automotive pillar products, with the advantages of reducing costs and increasing efficiency.
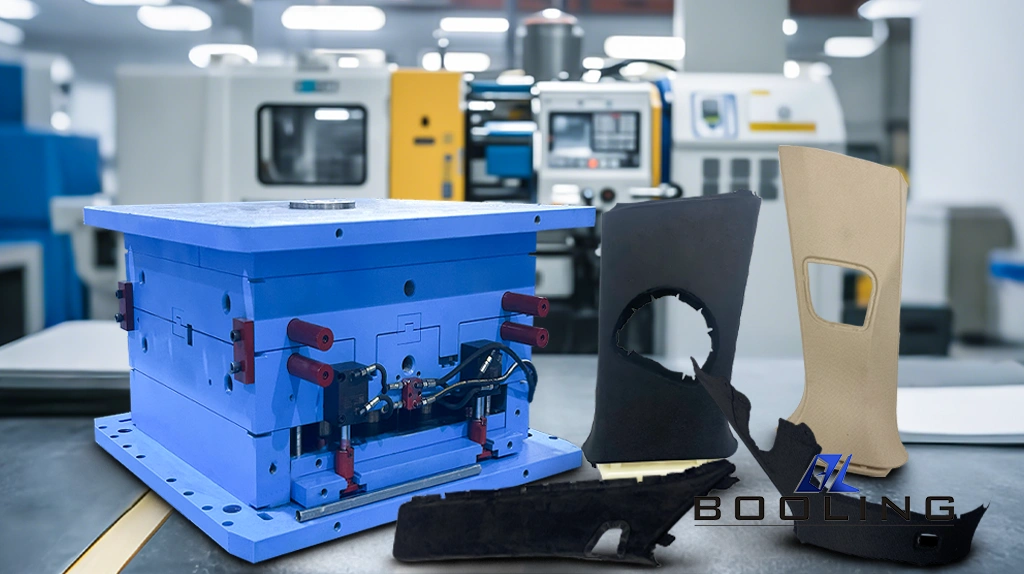
Types of Car Pillar Mold
Car pillar molds are mainly divided into three types: A-pillar (front windshield support), B-pillar (load-bearing structure between doors), and C-pillar (rear support). They are composed of plastic parts and metal parts. While providing interior aesthetics, they provide connection and support for the car body, which directly affects the safety and assembly quality of the whole vehicle. Booling’s technical expert team pointed out: “Modern pillar mold design is facing the dual challenges of lightweight and high strength. Our multi-material composite solution can meet both structural safety and aesthetic requirements.”
-A-pillar: Located on both sides of the car’s front windshield, it supports the front wall and roof of the vehicle and can effectively absorb and disperse the impact force when the vehicle collides. The car A-pillar products produced by our company’s molds can effectively reduce the deformation risk caused by the front collision of the vehicle and provide safe and reliable protection for the driver and passengers.
-B-pillar: Connects the roof and chassis, supports the roof, and disperses the side impact force. When the vehicle is hit, it can prevent the door from excessive deformation and protect the driver and passengers.
-C-pillar: Located between the rear door and the rear windshield, it is mainly used to support the rear of the roof and fix the rear window, and can maintain the stability of the vehicle body during driving.
-D-pillar: Some SUVs or large models will be designed with a D-pillar, located at the rear of the vehicle, which can further enhance the structural strength and stability of the rear of the vehicle body. Our company keeps up with market demand and actively develops D-pillar molds.
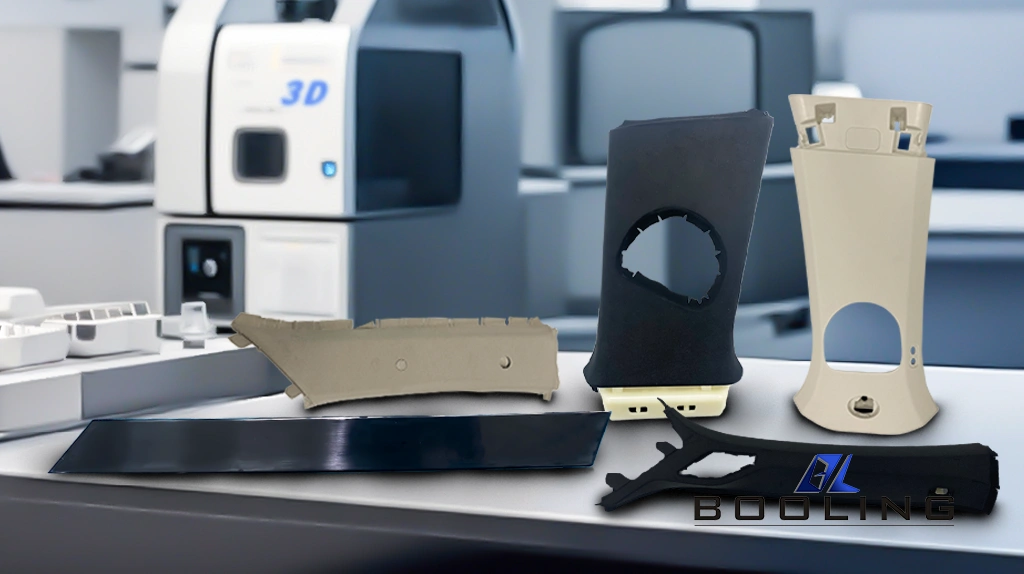
Automotive Pillar Mold & 3D Printing Technology
With the help of 3D printing technology, our company can quickly convert the digital model of the automotive pillar mold into a physical model, realize rapid prototyping, and provide a full-process solution for the automotive industry. “Under the trend of integrated die-casting of new energy vehicles,” said Booling, director of additive manufacturing, “our 3D printing technology can quickly verify the feasibility of large pillar molds and help customers seize the market opportunity.” We are committed to providing the automotive industry with smarter and more efficient mold manufacturing solutions to help customers achieve a rapid leap from concept to mass production.
Through 3D printed rapid prototyping, manufacturers can more intuitively check and evaluate the appearance and assembly relationship of the mold, ensure the feasibility of the solution, and optimize the design to reduce the weight and complexity of the mold.
3D printing technology has a short manufacturing cycle, can be directly based on the design model for rapid prototyping, and can achieve rapid production of small batches of products.
Automotive pillar molds have more complex shapes and structures. Traditional processing technologies and manufacturing methods have greater difficulty and higher costs in processing. Using 3D printing technology can achieve on-demand manufacturing, reduce processing costs, and easily achieve integrated manufacturing.
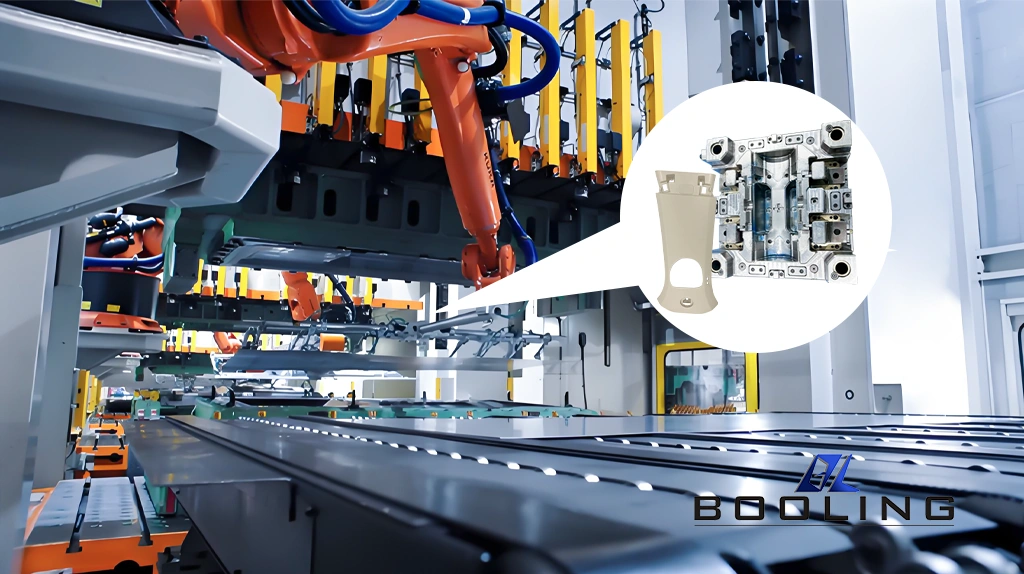
Digital Processing of Automobile Pillar Mold
In the field of automobile parts manufacturing, the accuracy of the pillar mold directly determines the safety and appearance consistency of the whole vehicle. Booling Company pointed out with its profound industry experience: “The accuracy standard of modern automobile pillar molds has been raised to ±0.03mm, which poses an unprecedented challenge to mold design and manufacturing.”
- Designers use computer-aided design software to accurately construct the three-dimensional model of the car pillar mold, clarify the details of each part of the mold, and determine the processing technology and processing procedures.
- Select suitable processing tools and set cutting parameters, speed, feed rate, cutting depth, etc. to ensure processing efficiency and quality and avoid tool wear.
- Use computer software to convert the set process and parameters into CNC code, generate tool paths, control machine tool movement, and realize milling, drilling, and other processing.
- Use a three-coordinate measuring instrument to accurately detect the size of the mold, and a laser scanner can quickly obtain three-dimensional data of the mold surface for comprehensive quality inspection.
Booling has more than ten years of rich experience in the design, processing, and testing of automotive pillar molds. It has provided more than 500 sets of molds to 46 manufacturers around the world, and the qualified rate of product delivery has remained above 99.8%. Through continuous innovation, Booling has provided pillar mold solutions that meet the IATF 16949 standard to many well-known global automakers, while ensuring collision safety and perfectly meeting the OEM’s strict requirements for appearance matching (gap and face difference ≤ 0.5mm). We are driving the industry towards a smarter and more precise direction.
Automotive Mold Related Content
Applied’s expertise in modifying materials at atomic levels and on an ihdustrial scaleenables our customers to transform possibilities into reality.