Home > Auto Bumper Mold: Five-axis Machining Technology
Details
Details:
Model
Material
Brand
Origin
Application
Booling-Automotive Mold-1
P20, 718, S136, 2738 etc
Booling
China
Automotive parts
When manufacturing car bumper molds, we always practice the core concept of “structural innovation drives quality revolution”. We know that “the complexity of bumper molds is not an obstacle, but a stage to show technical strength.” Therefore, Booling uses industry-leading five-axis machining technology to turn the curved surface structure that was traditionally considered impossible into reality.
Advantages of auto bumper mold processing
- High-efficiency production
- High precision
- Wide selection of materials
- Ability to achieve mass production
Related Hot Products
The material selection, design, and processing of auto bumper molds directly determine the quality of the final product. Booling analyzes parameters such as product structure, production process, and batch size, and introduces advanced high-precision five-axis linkage machining centers to achieve customized designs for different models, such as sedans, pickups, luxury sports cars, SUVs, etc., to meet users’ requirements for bumper quality and aesthetics.
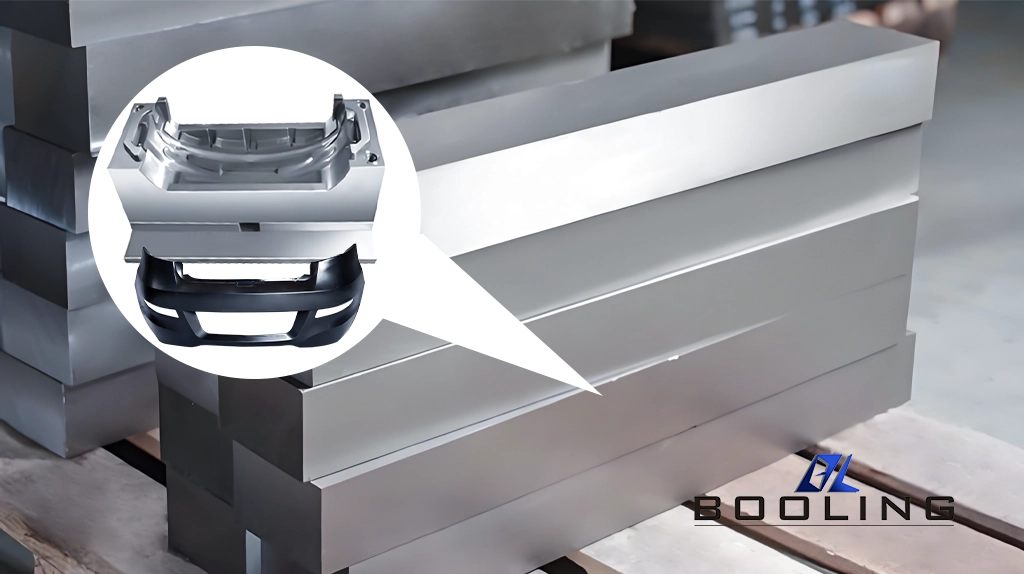
Selection of Auto Bumper Mold Materials
Booling has established strict acceptance requirements for the selection of steel materials, and has strict standards for steel materials such as S136, 718, P20, and NAK80, providing customers with cost-benefit analysis and steel performance comparison. Booling firmly believes that: “There is no best steel, only the most suitable solution.” We conduct quantitative analysis from eight dimensions such as wear resistance, polishability, and toughness to ensure that customers get the best balance between cost and performance.
-S136: S136 mold steel has good processing performance and polishability, and can be milled, ground, and other mechanical processes. Appropriate heat treatment can help it obtain better hardness, strength, and toughness, and extend its service life. Booling usually uses this steel in molds that require mirror polishing.
-718: Suitable for the processing of auto bumpers, door panel molds, etc., widely used in large molds, with high strength and good toughness. It can be polished and has unique advantages for some products with high appearance quality requirements.
-P20: Suitable for the processing of bumper molds for family cars and sedans. It has high strength and hardness, and can effectively prevent defects such as deformation of the mold during processing and use.
-NAK80: Often used by manufacturers to manufacture large-scale auto bumpers and home appliance molds. It has high hardness and strength and can withstand the high pressure and filling rate during injection molding.
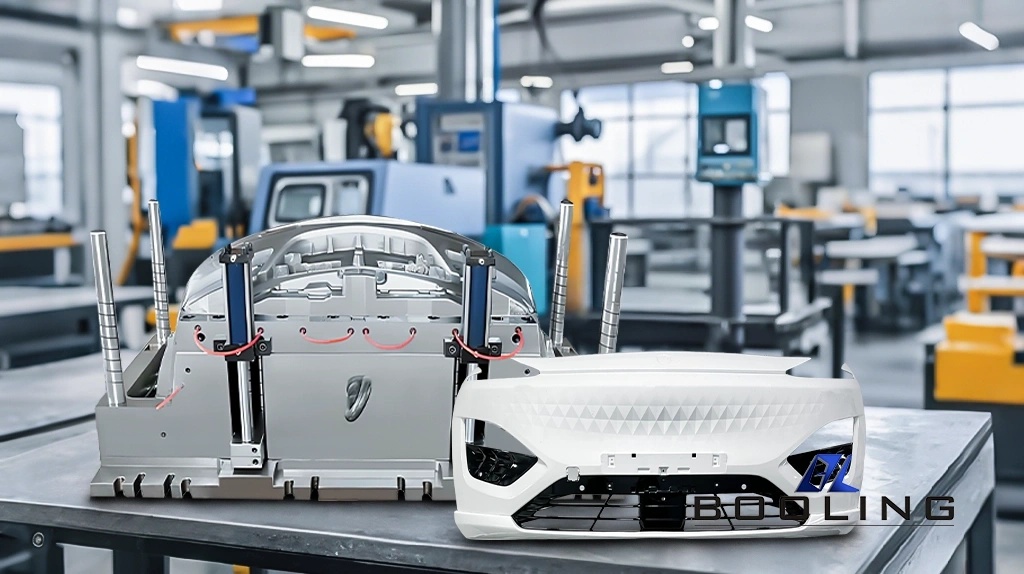
Design Principles of Auto Bumper Mold
In the design of auto bumper molds, Booling ensures that the product can be smoothly molded by considering the selected process, processing parameters, and other factors, and provides users with more professional quality improvement solutions. Booling always practices the core value of “design determines the upper limit of manufacturing”. We firmly believe that “excellent mold design is not a paper talk, but the best balance between manufacturing feasibility and product perfection.” Through the original “DFM (Design for Manufacturing)” system, Booling deeply integrates manufacturing factors such as process parameters and processing characteristics into the design front end.
- As an exterior component of the car, the bumper has high requirements for precision and appearance. Booling simulates the molding process of the mold through mold flow analysis, optimizes all injection molding parameters, and ensures the dimensional accuracy of the molded product.
- Consider the quality of the mold during the processing process, ensure its wear resistance, impact resistance, and other properties, and be able to withstand strong impact and pressure during the processing process to extend its service life.
- Design a reasonable demolding mechanism to ensure that the molded bumper can be smoothly ejected from the mold to avoid defects such as deformation and strain, and ensure the appearance quality of the product. Booling provides ejection solutions such as push rods, push plates, and inclined ejectors, which are configured according to the specific needs of users and products.
- Booling provides options such as point gates, latent gates, and bullhorn gates to improve processing efficiency while improving the surface quality of products.
- Booling has established a special processing schedule for each mold to provide data guarantee and picture tracking for subsequent maintenance.
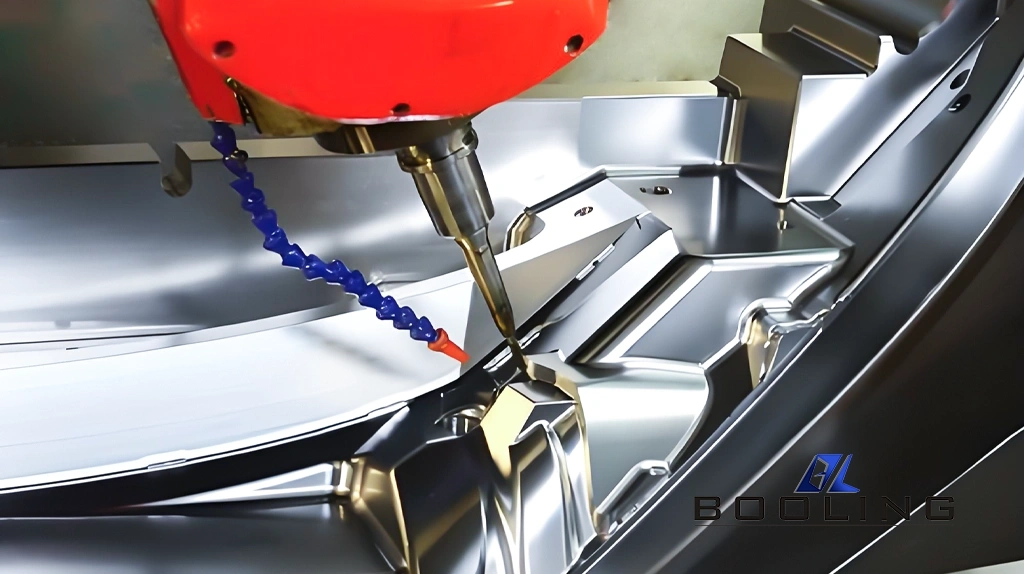
Processing of Auto Bumper Molds
Booling’s auto bumper molds undergo rough machining, fine machining, heat treatment, and other processes, which can increase the process life by more than 30%. We use the intelligent linkage system of “machining parameters-tool life-quality performance” to ensure that each processing link reaches the optimal state. Because we know that excellent mold technology is a solid guarantee of customer competitiveness.
-Rough machining: Booling uses five-axis linkage CNC machine tools and other equipment to implement turning, milling, and other processes to perform rough machining on the mold and remove most of the blank residue of steel. For more complex auto bumper molds, layered cutting can be performed according to the contour lines of the parts to improve processing efficiency. The material removal rate of our rough machining can reach more than 98.5%.
-Fine machining: Use CNC machining, EDM machining, wire cutting, and other processes to perform three-dimensional curve fine machining on the mold, and use professional abrasives to remove the tiny residue on the mold surface to improve the processing quality of the mold.
-Heat treatment: Through tempering, vacuum quenching, and other processes, the internal structure of the mold is changed to improve the toughness, wear resistance, and other properties of the mold.
We adopt innovative modular production management solutions, and through intelligent scheduling systems and digital production chains, we can greatly shorten the production cycle. Choosing Booling is not only choosing high-quality auto bumper molds but also choosing a trustworthy strategic partner.
Automotive Mold Related Content
Applied’s expertise in modifying materials at atomic levels and on an ihdustrial scaleenables our customers to transform possibilities into reality.