Home > Auto Door Panel Mold | Automotive Parts Manufacturing
Details
Details:
Model
Material
Brand
Origin
Application
Booling-Automotive Mold-1
P20, 718, S136, 2738 etc
Booling
China
Automotive parts
An excellent door panel mold should not only realize the molding of complex structures but also reserve perfect interfaces for subsequent assembly. Our modular core-pulling mechanism not only improves production efficiency by 20% but also ensures accurate matching of product dimensions so that each door panel product can perfectly meet the assembly requirements of the whole vehicle. As a large exterior component, the structural design and manufacturing process of the mold directly determines the appearance and quality of the terminal product. Booling adopts a composite slider linkage solution and modular core-pulling mechanisms to achieve easy molding of complex structures.
Advantages of door panel mold processing:
- High efficiency
- Consistent molding
- Integrated molding
- High processing accuracy
Related Hot Products
Our automotive door panel molds rely on the analysis and simulation technology of the digital platform to optimize the gate layout, water channel, ejection system, and other structures in multiple dimensions. Engineers improve the production efficiency and yield rate of molds by real-time monitoring and optimizing parameters such as temperature, time, and pressure. Our engineering manager said that the molds we provide to users are always quality-first. We are well aware that “the degree of intelligence of the mold determines the competitiveness of manufacturing.” Booling will continue to promote digital transformation and use smarter mold solutions to help customers gain an advantage in the fierce market competition.
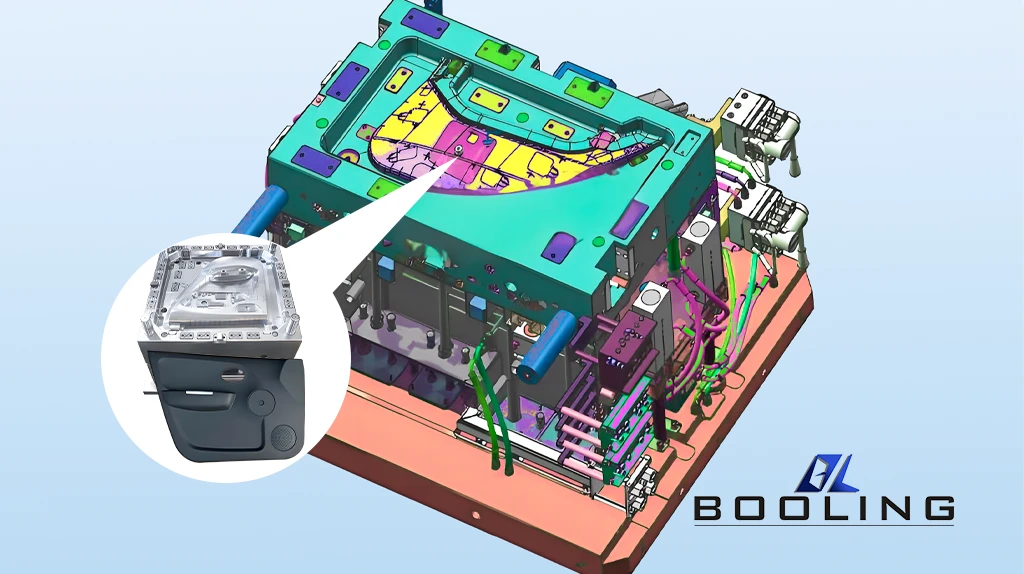
Design Optimization of Automobile Door Panel Mold
In the field of automobile parts manufacturing, Booling, as an industry-leading mold designer and manufacturer, continuously improves the quality of automobile door panel products by optimizing mold design. We have established a complete digital mold life cycle management system. Through real-time monitoring and intelligent optimization of key parameters such as temperature, time, and pressure, our mold production efficiency has increased by 25%, and the yield rate has remained stable at more than 99.5%. This pragmatic style of “speaking with data and proving with results” is the root of Booling’s trust in global customers.
- Use an intelligent analysis system to study 3D models, deeply understand their shape, size, wall thickness, and other parameters, and communicate and understand parameters such as production batch and quality requirements.
- According to the appearance requirements of the door panel, reasonably select the parting surface to ensure smooth opening and closing of the mold and smooth demolding.
- Automobile door panels are large products, and the corresponding molds are large. It is necessary to design a cooling system that is as efficient as possible and keep the layout of the cooling water channel reasonable. Our engineers suggest that circulating water channels and other forms can be used to ensure the cooling efficiency of large products.
- Door panels have high requirements for appearance quality. When choosing the type of gate, side gates, latent gates, etc. are often selected to improve the aesthetics. For large door panels, multi-point feeding can be used for processing.
- For large door panel molds, the layout of ejectors needs to be sufficient and uniform to ensure that the product can be demolded smoothly without causing deformation or scratching the product, resulting in product scrapping.
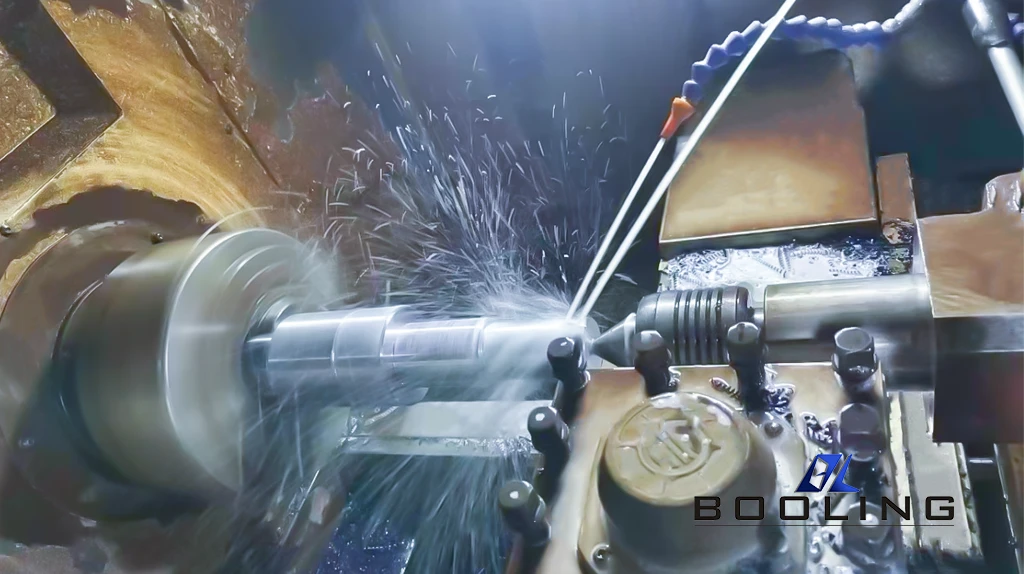
Optimization of Automobile Door Panel Mold Processing Technology
In the field of automobile parts manufacturing, the accuracy of automobile door panel molds directly affects the quality and production efficiency of products. Booling strictly follows the three-step processing system of roughing, semi-finishing, and finishing processes: roughing lays the foundation, semi-finishing optimizes the structure, and finishing ensures perfection. We firmly believe that “without strict process discipline, there will be no excellent product quality”, so each set of door panel molds at Booling strictly follows the process standards and technical specifications.
Within the range allowed by the equipment performance, we try to use high-speed processing to improve cutting speed, feed rate, processing efficiency, and surface finish. At the same time, use intelligent algorithms to optimize tool paths to avoid errors and wear.
Our company is equipped with a professional heat treatment workshop. For different mold steels, we formulate heat treatment plans, such as tempering and quenching, to improve the overall performance of the mold, such as hardness and toughness. For some high-performance mold steels, multiple tempering methods can be used to eliminate the internal stress of the mold.
In the surface treatment link, we have a variety of processing processes such as mirror polishing, nitriding, chrome plating, leather graining, etc., to extend the service life of the mold and improve the mold hardness, wear resistance, and corrosion resistance.
Use higher precision processing equipment to improve the degree of automation and reduce human errors, such as five-axis CNC machine tools, EDM machines, wire cutting machines, etc., to reduce human intervention and minimize human errors.
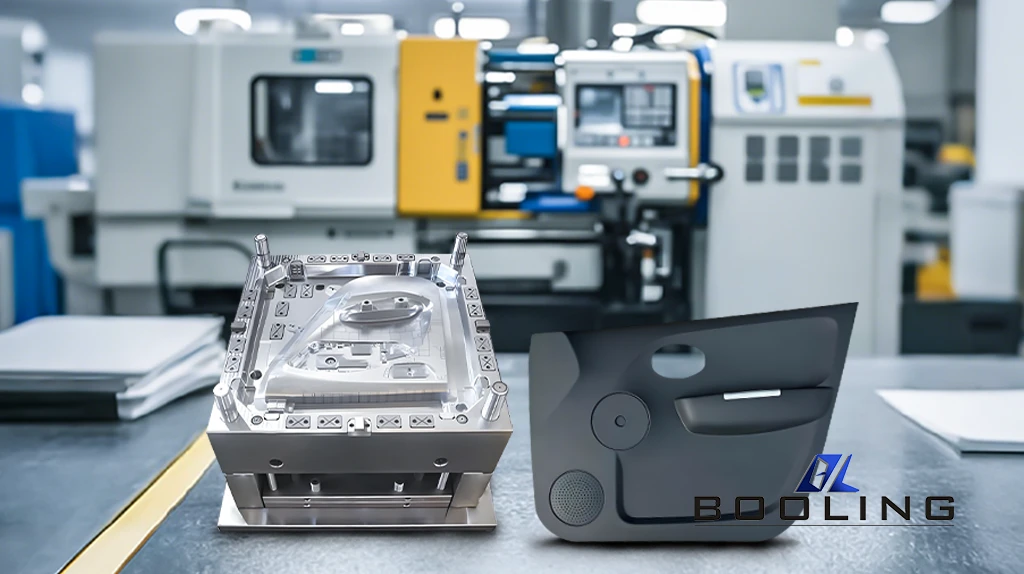
Optimization of Assembly Process of Automobile Door Panel Mold
Our engineers believe that improving the assembly accuracy of automobile door panels is conducive to reducing the defective rate of products and significantly improving the market competitiveness of users. As our engineering team emphasized: “Improving the assembly accuracy of automobile door panels is not only a technical indicator but also a quality commitment to end users.” We firmly believe that every micron of accuracy improvement will be transformed into a significant advantage in the customer’s market competitiveness.
Before formally assembling the mold, the mold is thoroughly cleaned to remove oil and impurities generated or remaining during the processing process to prevent parts from rusting during assembly and storage and affecting the assembly quality.
According to product requirements and mold selection interchange method, grouping method, repair method, and adjustment method for assembly improve overall assembly efficiency and accuracy.
Adopt automated assembly solutions to avoid assembly errors. Use rapid positioning and clamping technology to achieve rapid positioning of parts and reduce assembly auxiliary time.
Establish a strict quality and tolerance control system and keep detailed records so that the cause can be traced back and improvement measures can be taken later.
Our company always adheres to customer needs as the ultimate guide and technological innovation as the driving force to provide high-quality and high-performance mold solutions for users in the automotive industry. At Booling, we not only manufacture automotive door panel molds but also strive to create sustainable competitive advantages for our customers, because “real quality will always stand the test of the market”.
Automotive Mold Related Content
Applied’s expertise in modifying materials at atomic levels and on an ihdustrial scaleenables our customers to transform possibilities into reality.