Home > Automobile Checking Fixtures | BOOLING Automobile Mould Manufacturing Process
Details
Details:
Model
Material
Brand
Origin
Application
Booling-checking-fixture-1
P20, 718, S136, 2738 etc
Booling
China
Home Appliance parts
In the field of automotive parts manufacturing, Booling can accurately and efficiently detect the quality and precision of automotive parts through the research and development and manufacture of automotive checking fixtures. During the design and manufacturing process, Booling’s engineering team sets reasonable positioning and clamping solutions, uses advanced 3D simulation technology, and accurately plans positioning points and clamping methods, so that it has sufficient rigidity and test stability, improving the accuracy of mold processing.
Necessity of checking fixtures testing:
- Improve product accuracy
- Have repeatability
- Avoid manual measurement errors
- Improve product processing efficiency and pass rate
Booling checking fixtures use fast positioning and clamping mechanisms, such as pneumatic locking and magnetic adsorption, to control the single-piece checking time within 15 seconds, meeting the efficient production needs of the automotive industry. We always adhere to a strict quality management system, and the quality of the automotive checking fixtures we produce is stable and reliable and can remain usable for a long time, meeting the automotive industry’s requirements for component accuracy.

Design Requirements for Automobile Checking Fixtures
In the field of automobile manufacturing, efficient and accurate testing is the key to ensuring product quality and production efficiency. Booling automotive checking fixtures always meet strict usage standards and provide a full range of measurement solutions.
- Productivity Requirements
Booling’s automotive checking fixtures use a variety of fast and efficient assembly mechanisms to meet the production efficiency requirements of precision automotive parts, assist automotive assemblers in achieving rapid assembly, and provide guarantees for the production and checking efficiency of the Entire Vehicle.
- Ability to achieve an effective evaluation of the quality of automotive parts
Whether the automotive checking fixture can effectively judge the parts depends on whether it has effective positioning references, methods, and positioning elements. Booling determines each positioning reference point by combining three-coordinate measurement technology to fully meet the strict requirements of automotive parts quality.
- Ensure the Performance of the checking Fixture
The checking fixture designed by Booling adheres to the humanized design, which is labor-saving, safe, and reliable, and a single person can complete the checking operation of the parts. At the same time, mechanical clamping methods such as pneumatic or hydraulic are used to avoid manual clamping to ensure the safety and stability of the test.
- Standardized Components
In the design process of automotive checking fixtures, standardized components can be appropriately used to improve the versatility and interchangeability of the checking fixtures, avoid long-term maintenance, and reduce maintenance costs.
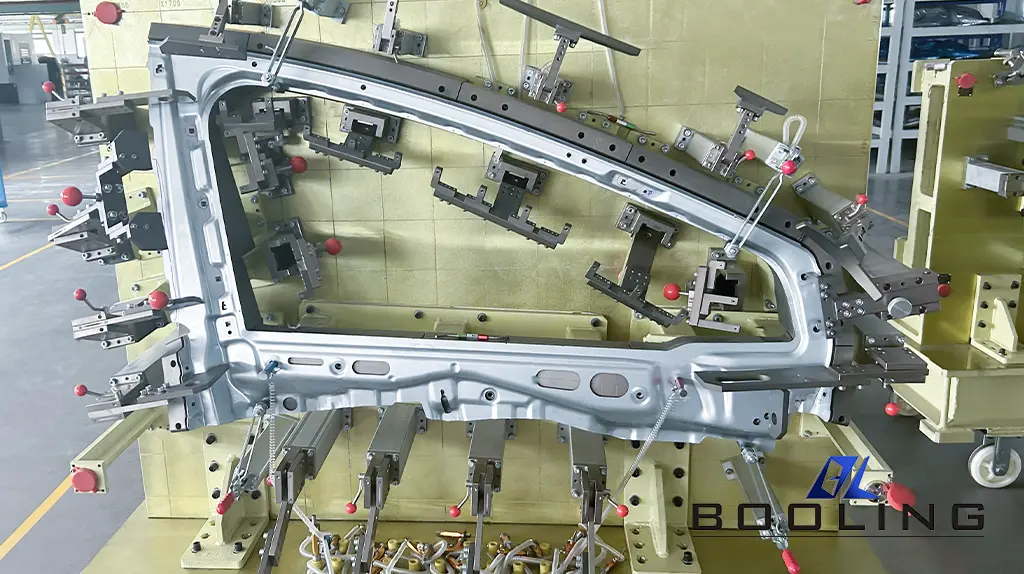
Design Process of Automobile Checking Fixture
In the field of automobile manufacturing, efficient and accurate testing is the key link to ensure product quality and production efficiency. Booling automotive checking fixtures always meet strict usage standards and provide a full range of measurement solutions. As an industry-leading checking fixture manufacturer, we believe that: “Excellent checking fixture design should not only meet current testing needs but also reserve upgrade space for future intelligent manufacturing.”
- Clarify design requirements
Booling adheres to the concept of “demand-driven design”, clarifies the design requirements and uses of checking fixtures, and conducts a precise analysis of the information and tolerance range of the tested products.
- Clarify the specific design requirements of automotive checking fixtures
Our engineers will select appropriate testing solutions based on the structural characteristics and monitoring requirements of the parts and determine whether to use contact testing. According to the degree of automation of the user’s workshop, formulate differentiated testing strategies.
- Determine the positioning system
Our company uses a high-precision one-sided two-pin positioning system to ensure that the positioning repeatability error of parts is within 0.01mm.
- Digital design solution
Use professional three-dimensional design platforms such as UG to achieve digital management of the entire process from conceptual design to engineering drawings.
- Proofreading
Proofread all parts according to the drawings, simulate and test the feasibility of the design, and ensure that all parts can be fully coordinated.
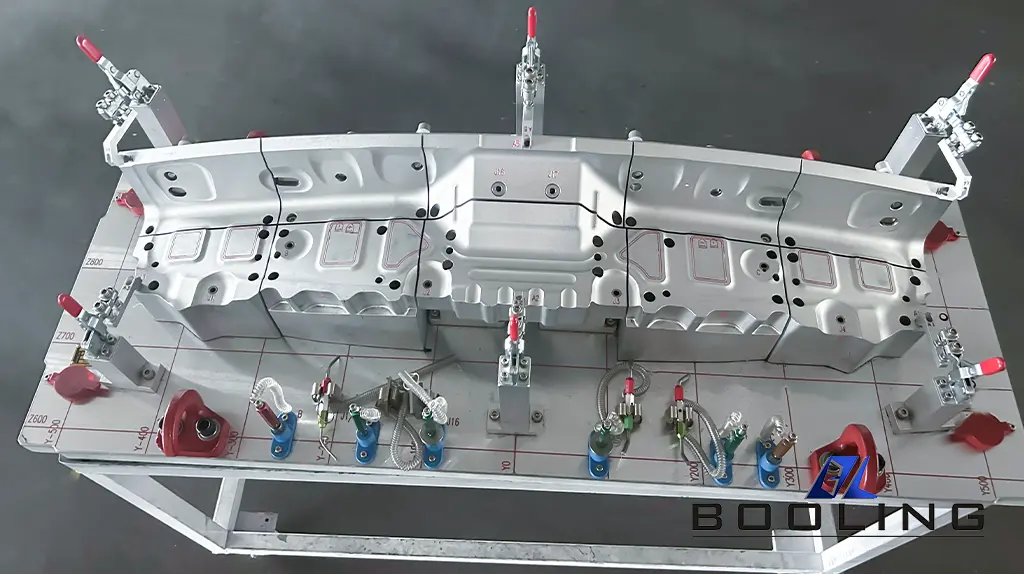
Review Scheme For Automobile Checking Fixture Design
The design of automotive checking fixtures should fully consider ergonomics, adopt modular design to simplify the assembly process, and have higher production efficiency. And use the three-coordinate measuring machine to check and ensure accuracy.
- Our engineers use the three-coordinate measuring machine to accurately measure the key dimensions and form and position tolerances, and compare them with the design values. If the deviation exceeds the allowable range, timely adjustments and corrections will be made.
- Our company will select suitable materials according to the specific use environment and testing requirements of the automotive checking fixture, and select the most cost-effective material selection plan to ensure the service life, reliability, and repeatability of the checking fixture.
- The designer will use detailed icons to clearly explain and confirm the final test method, including product quality characteristics, key product characteristics, process monitoring points, functional holes, characteristic lines, and parts prone to wear, to improve production efficiency and quickly find abnormal characteristics.
Booling’s review process has specially added a “customer perspective simulation” link, in which a dedicated user experience team simulates the customer’s on-site usage scenario. As our chief technology officer said: “True quality is not measured in the laboratory, but verified on the customer’s production line.” Through such a strict review system, we ensure that every set of checking fixtures shipped out of the factory can perfectly match the actual needs of customers.
Booling always believes that: “Excellent fixture design is the perfect combination of the manufacturing process and testing technology.” We not only provide fixture products but also provide complete quality solutions to help customers achieve closed-loop improvement from testing to process optimization. Through continuous innovation, our fixture design has obtained more than 20 technical patents and served more than 50 world-renowned automobile manufacturers.
3D Printing Service Related Content
Applied’s expertise in modifying materials at atomic levels and on an ihdustrial scaleenables our customers to transform possibilities into reality.