Home > Injection Molding > Insert Molding Service
The perfect nesting solution for metal and plastic
- Dozens of expert teams respond quickly and provide solutions
- Many well-known manufacturers partners
- Strict Privacy Mechanism
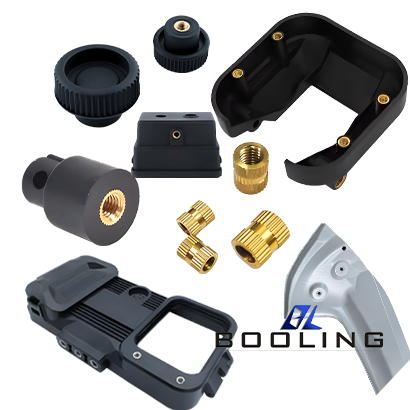
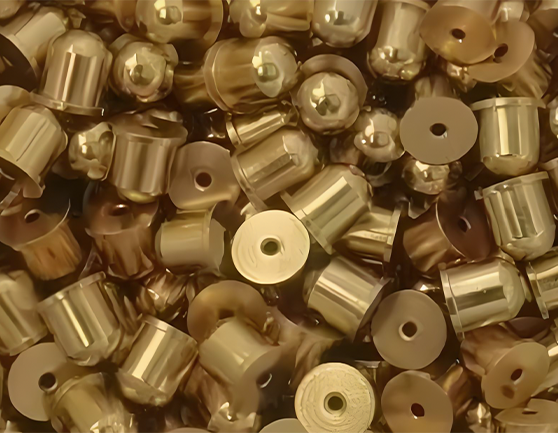
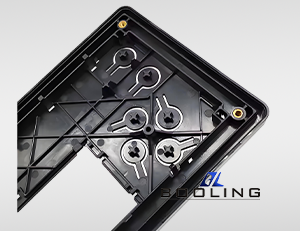
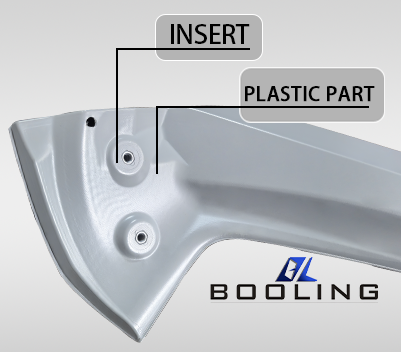
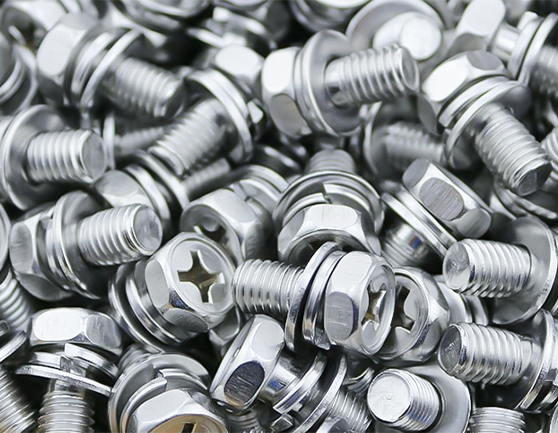
Insert Molding Service
BOOLING insert molding process is a solution that combines plastic parts and metal parts. Metal parts, electronic parts, ceramic parts or other materials can be embedded into plastic workpieces through single injection molding, which can greatly increase the functionality and structure of the product and improve the product assembly efficiency of partners.
BOOLING has served multiple fields such as electronics, automobiles, medical, home appliances, and daily chemicals with this technology. We have dozens of experienced engineers and are equipped with the current international mainstream manufacturing equipment and software. From design to mass production of products, Booling’s insert molding technology can provide the best and most efficient solutions for your application field.
- Copper terminals (conductive)
- stainless steel screws (structural)
- Preformed fiber reinforcements
- Sensor insulation base
- Screws
- PCB board
- chip carrier
What is insert injection molding?
Insert molding is a process that involves embedding prefabricated inserts into plastic workpieces through a single injection molding process. This process can integrate metals, plastics, ceramics or other materials into an integrated form, solving the complexity of manual assembly and providing product structural strength and precision.
Our Insert Molding Application Examples
Plastics inlaid with metal, glass, wood, fiber, paper, rubber or molded plastic parts are called inserts, and the most common inserts are metal.
Since the combination of plastic parts and other materials needs to ensure a certain degree of compatibility, such as copper (17 ppm/°C) and PPS (30 ppm/°C), Booling will give priority to whether the thermal expansion coefficients of the inserts and plastics to be matched are compatible. If there is a repulsion problem between the two, our engineers will compensate through a series of designs during mold design.
- Connector (metal terminal + insulating plastic)
- Endoscope handle (stainless steel + medical PC)
- Carbon fiber insert + PEI composite material
- Sensor housing (metal shell + PA66)
- Washing machine counterweight (cast iron + PP)
Material Selection For Insert Molded Parts
Inserts are usually metals, ceramics, electronic components or other prefabricated parts. We mainly complete the entire insert molding process by embedding such materials into plastic injection molded parts.
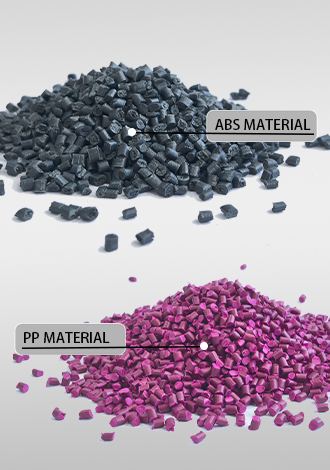
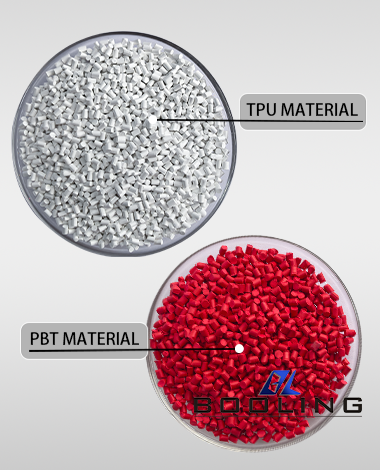
The selection of base materials for insert molding often needs to have good fluidity, bonding strength with the insert and adaptability to the terminal environment, which plays a vital role in the quality and structural strength of the final product.
Based on the materials selected by customers, BOOLING provides the following:
1. ABS: It is mainly suitable for the production of electronic housings, such as keyboard buttons, remote control housings, etc., especially because of its low heat resistance, we usually do not recommend it for high-temperature inserts.
2.PP: PP material is used in many applications, such as our car battery box, power strip, etc., mainly because of its special chemical properties, but it should be noted that the polarity of this material is low, and we usually do corona treatment on the surface of the insert.
3. PA66: Nylon material is usually used in automotive gearbox inserts, mainly because of its high oil resistance and high rigidity, but generally we need to chemically modify it to make it compatible with the thermal expansion coefficient of metal to prevent incompatibility problems.
4. PBT: It is a translucent or opaque, crystalline thermoplastic polyester resin. Because PBT has the characteristics of arc resistance and low moisture absorption, it is usually suitable for manufacturing some electrical appliances, such as TV transformer parts.
5. PEEK: Polyetheretherketone is a relatively rare material, mainly used in some high-temperature resistant products, such as aircraft fuel valves, gas stoves, etc.
6. LCP: Liquid crystal polymer is a material with ultra-low warpage and thin-wall fluidity, which is mainly suitable for microelectronic packaging, such as 5G antenna module inserts.
LCP (liquid crystal polymer):
7. TPU: Thermoplastic polyurethane needs to be assembled through secondary injection molding or in-mold assembly. Due to its strong shock absorption effect, we recommend it for tool handles.
BOOLING insert molding service includes material selection. The most common ones are metal inserts, such as copper alloy, stainless steel, aluminum alloy, titanium alloy, etc. This mainly depends on whether the thermal expansion coefficient matches the plastic matrix and the surface roughness.
In addition to metal inserts, ceramics, engineering plastic preforms, electronic components, etc. also require insert molding processes. For example, ceramics have high insulation properties and are usually used to manufacture sensor substrates. We usually combine them with silane coupling agent treatment.
Of course, if you need other materials or more suggestions, you can also contact our engineers to get the best solution.
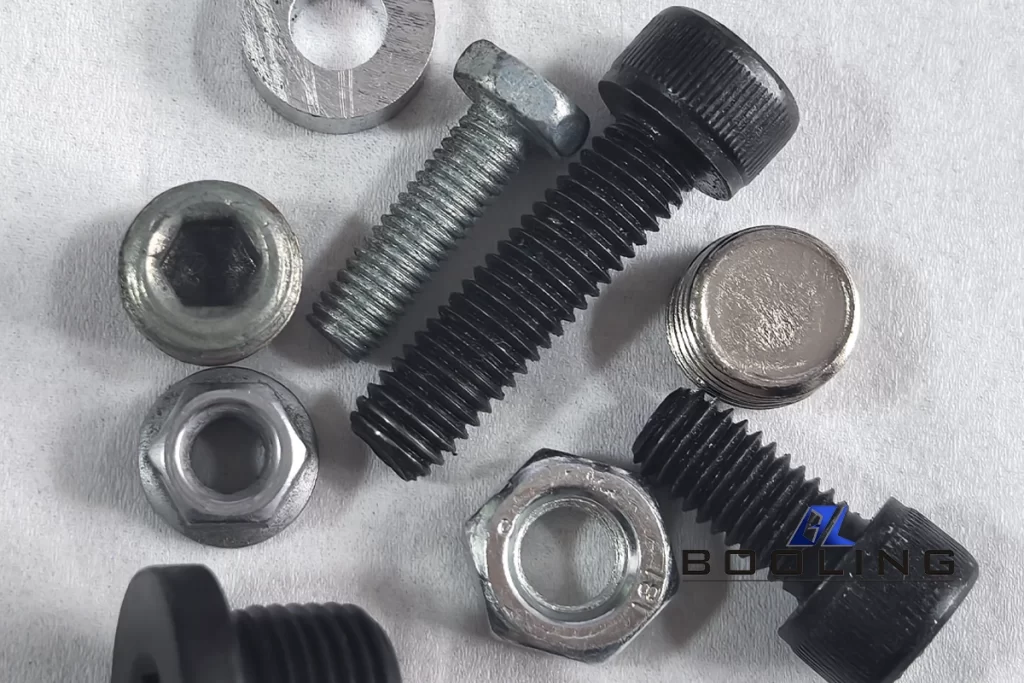
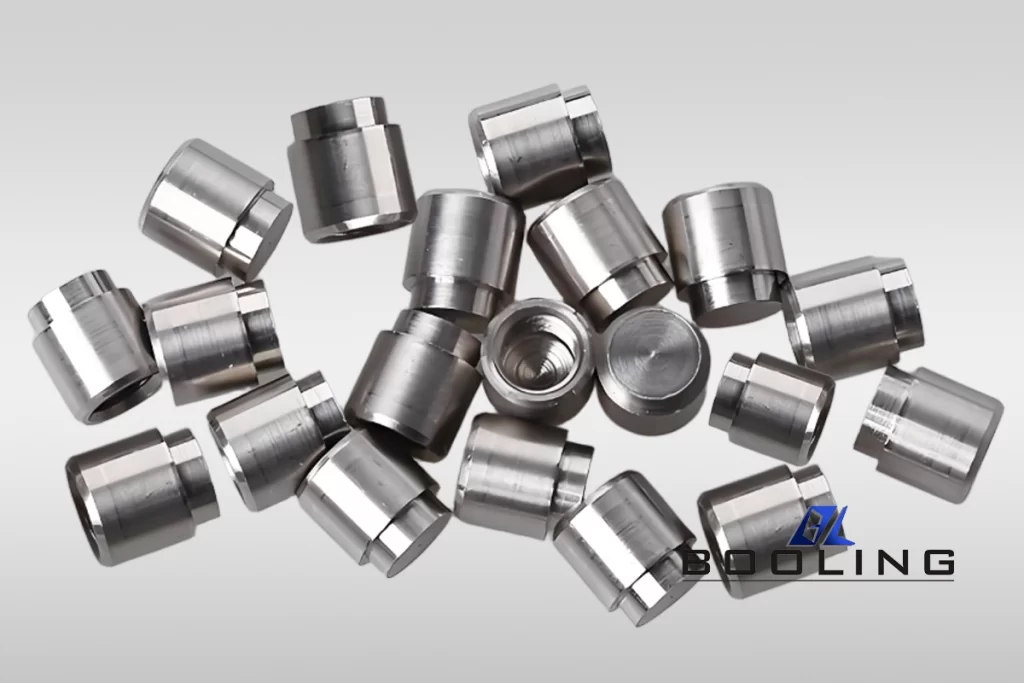
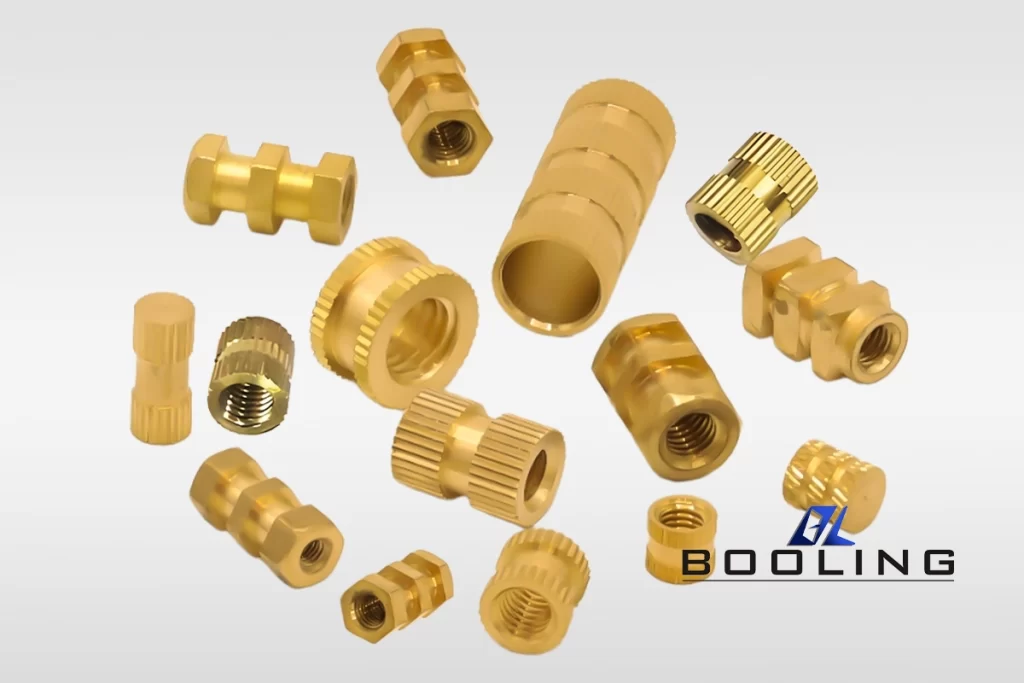
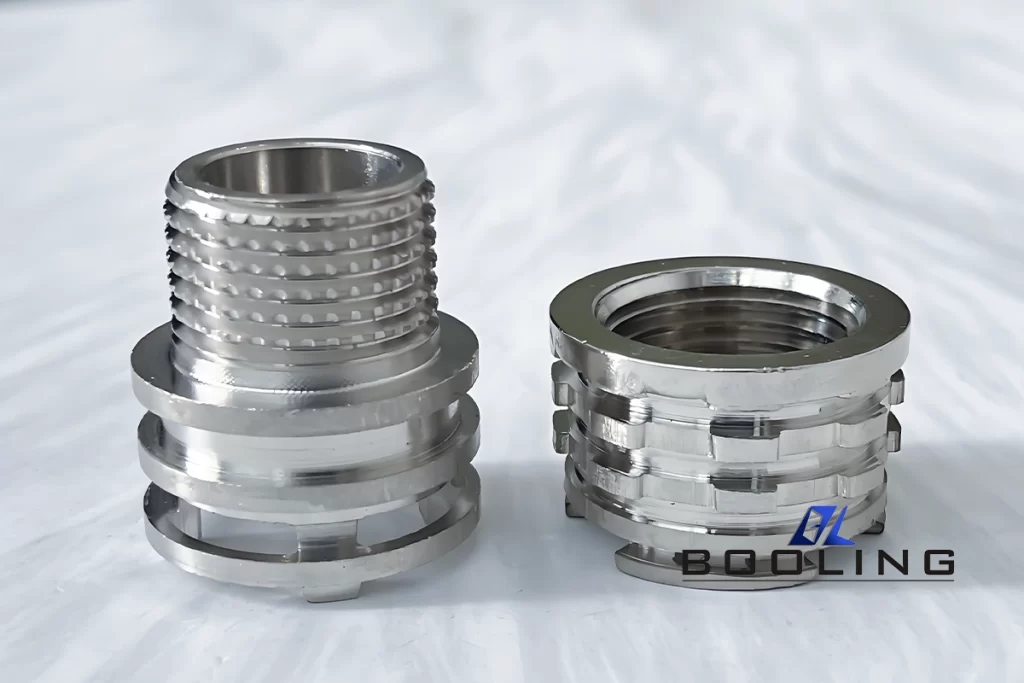
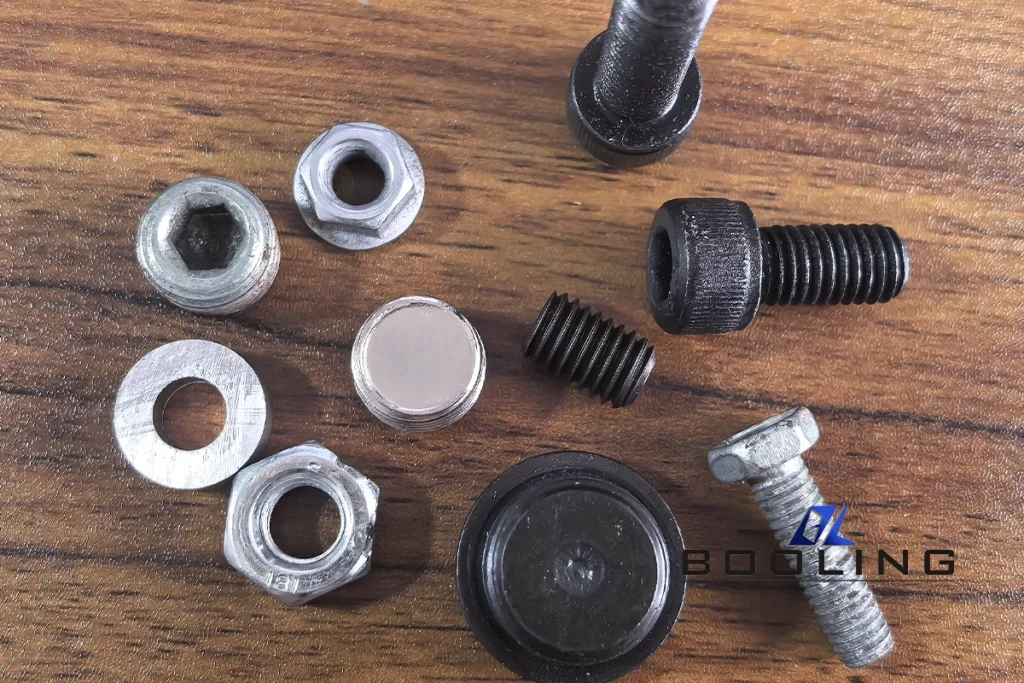
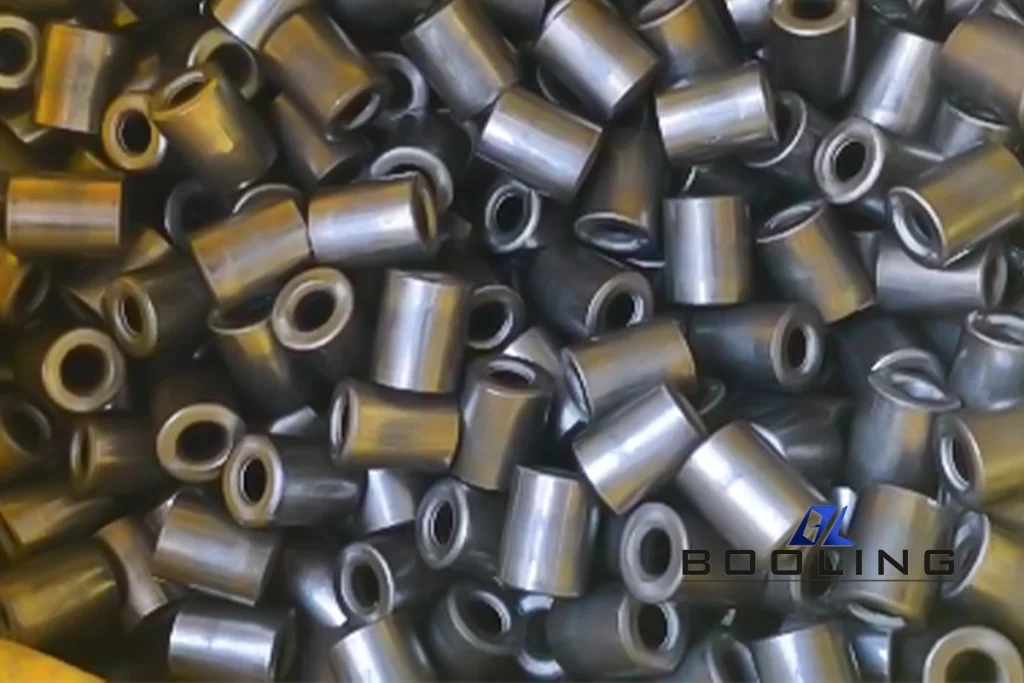